A host of big picture issues influence costs in the construction and development industry. But as any construction cost estimator will tell you, the devil is in the detail. Little things often make the biggest difference to whether a construction company is buoyant, or just busy and broke.
In mid-February, I unpacked the heaviest cost pressures weighing down construction companies These ranged from the top-of-mind issues – like site lockdowns, skills shortages and supply chain bottlenecks caused by Covid-19 – to the less obvious, such as the Suez Canal blockage, the collapse of Evergrande in China and emissions-reduction policies in Europe.
A lot has happened in two short months. Firstly, the obvious. Covid-19 and the close contact rules continue to be a state-by-state story that cause construction speed bumps in some local markets. But further afield, the latest travel restrictions and stay-at-home orders in China will hurt construction supply chains for months. Shanghai, for example, accounts for around 3.8% of China’s GDP but is also home to the world's busiest port.
The war in Ukraine has knocked the pandemic from the top spot in the news, intensifying shipping logjams, and sending commodity prices and inflation soaring. Commodity-rich Australia has been one of the few countries to benefit. This may be good news for the Australian Government’s bank balance, but bad news for civil engineering and excavation companies that have seen fuel costs rise by around a third.
Russia is the largest timber exporter in the world, and its decision to invade Ukraine has poured petrol on already eye-watering lumber prices. The federal government has slapped a 35% tariff on imports from Russia and Belarus, and certification bodies have deemed timber sourced from these countries ‘conflicted’. The situation has sparked interesting conversations about chain of custody, but ultimately, we must also count the costs.
Closer to home, war worries and pandemic panic have been supplanted by a more ordinary issue: weather. Sydney and its surrounding regions suffered 46 declared wet days in just over two months earlier this year. Contingency budgets have been soaked up and costs are soaring. On a $150 million job, we are talking about a $4 million cost courtesy of La Niña.
And that’s not even extreme weather. Almost 5,000 homes were deemed uninhabitable after the New South Wales and Queensland floods in March – significantly more than the 3,000 homes destroyed across Australia during the Black Summer bushfires in 2020. With the insurance bill from the floods now expected to exceed $3 billion, premiums are likely to rise by around 10%. The rebuilding program will drive further material cost blowouts too.
Meanwhile, unemployment is heading towards its lowest rate in half a century and job vacancies are above pre-GFC levels. Builders can’t find skilled subcontractors and when they can only for silly money.
Inflationary pressures continue to cause political headaches. While Australia’s cash rate remains low, inflation continues to soar at an even faster pace than anticipated. It is only a matter of time before the Reserve Bank acts. This will place obvious pressure on the purse strings of the third of Australians who are highly geared mortgage holders. As interest rates climb, people tend to turn to their boss for some extra dollars in their pay packet, which causes further cost blowouts.
Builders are weighing up the potential rewards on a set of scales unfairly tipped towards risk. Many are turning down projects – especially in the residential sector – that are simply not worth the gamble. Others are unable to take on new work because tens of millions of dollars are locked up in client security accounts for jobs completed months ago.
How do we find out way out of the profitless boom?
Construction companies can reach for a few levers: strategic procurement, contingency planning and careful risk management. Advance purchases and hedging supplies are among the few ways businesses can gain surety – although this is not an option open to every business as it further ties up cash flow.
Most construction costs are largely out of Australia’s control. But there is one colossal cost over which we do have some control and a lever that most other nations cannot pull. That cost is labour. And the lever? Migration.
It’s simple: a country built on migration needs migration to thrive. While international students are being used to plug some unskilled labour shortages, it is skilled workers that are in shortest supply.
We can take instantaneous steps to control our labour costs by widening the pool of available workers. But we must make haste. Other markets, like the United States and Canada, are also on the hunt for skilled workers. Getting on the front foot now will help us for years to come.
Author
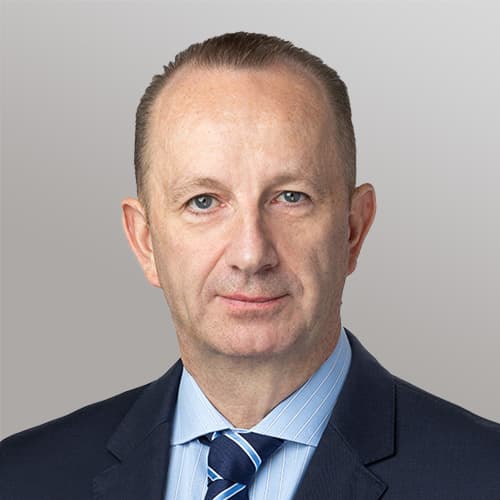
Niall McSweeney
Head of Development Advisory, Asia-Pacific
Author
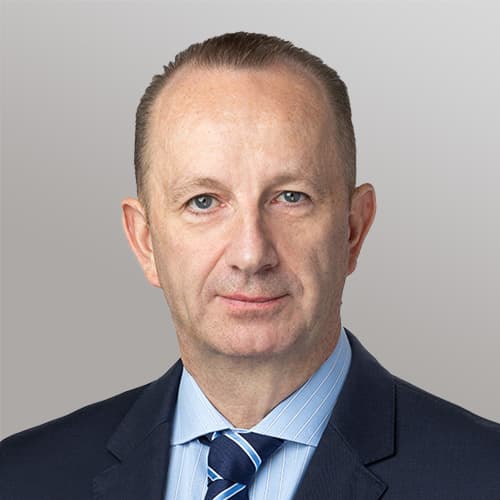
Niall McSweeney
Head of Development Advisory, Asia-Pacific
Resources
Latest insights
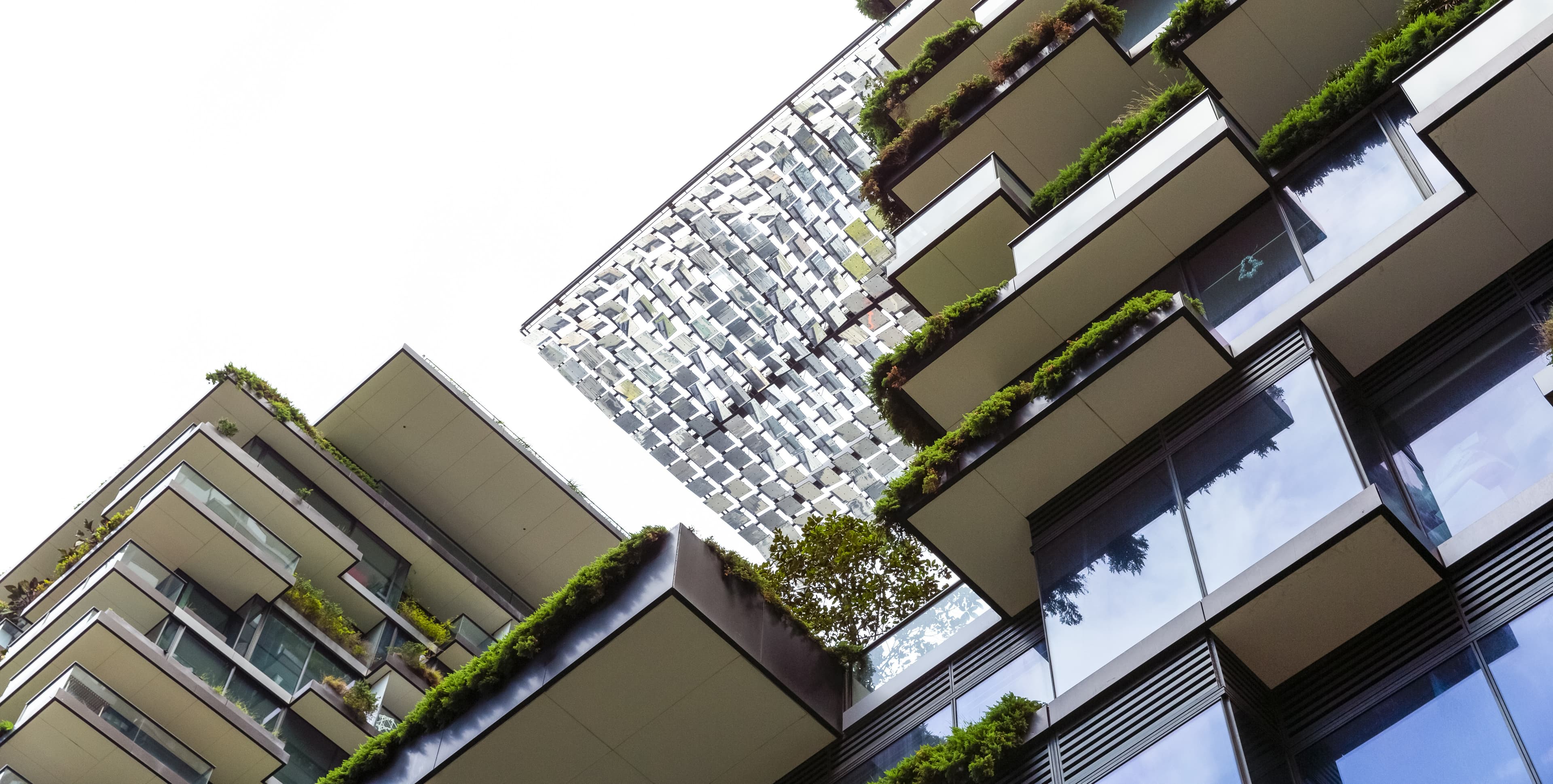
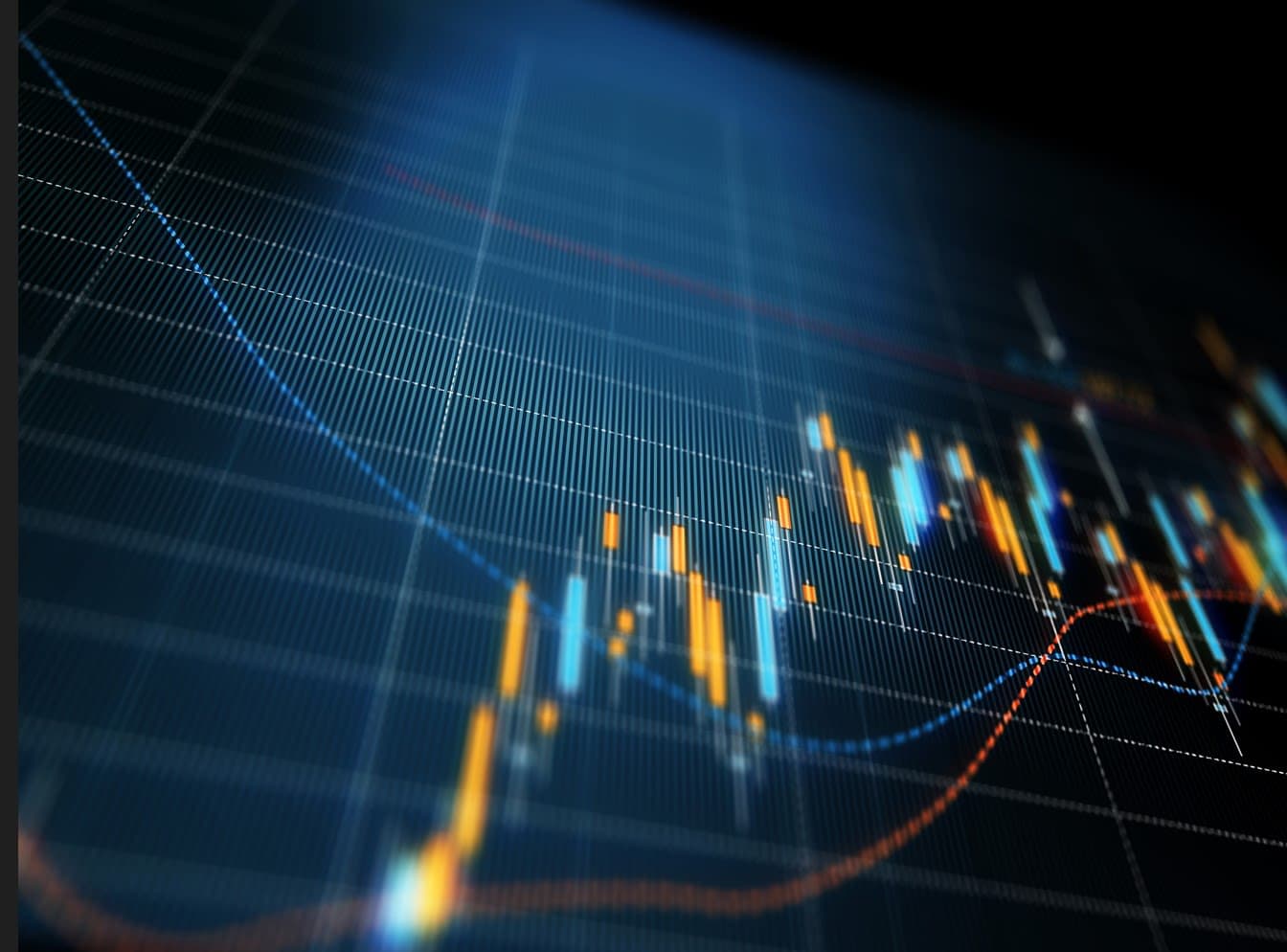
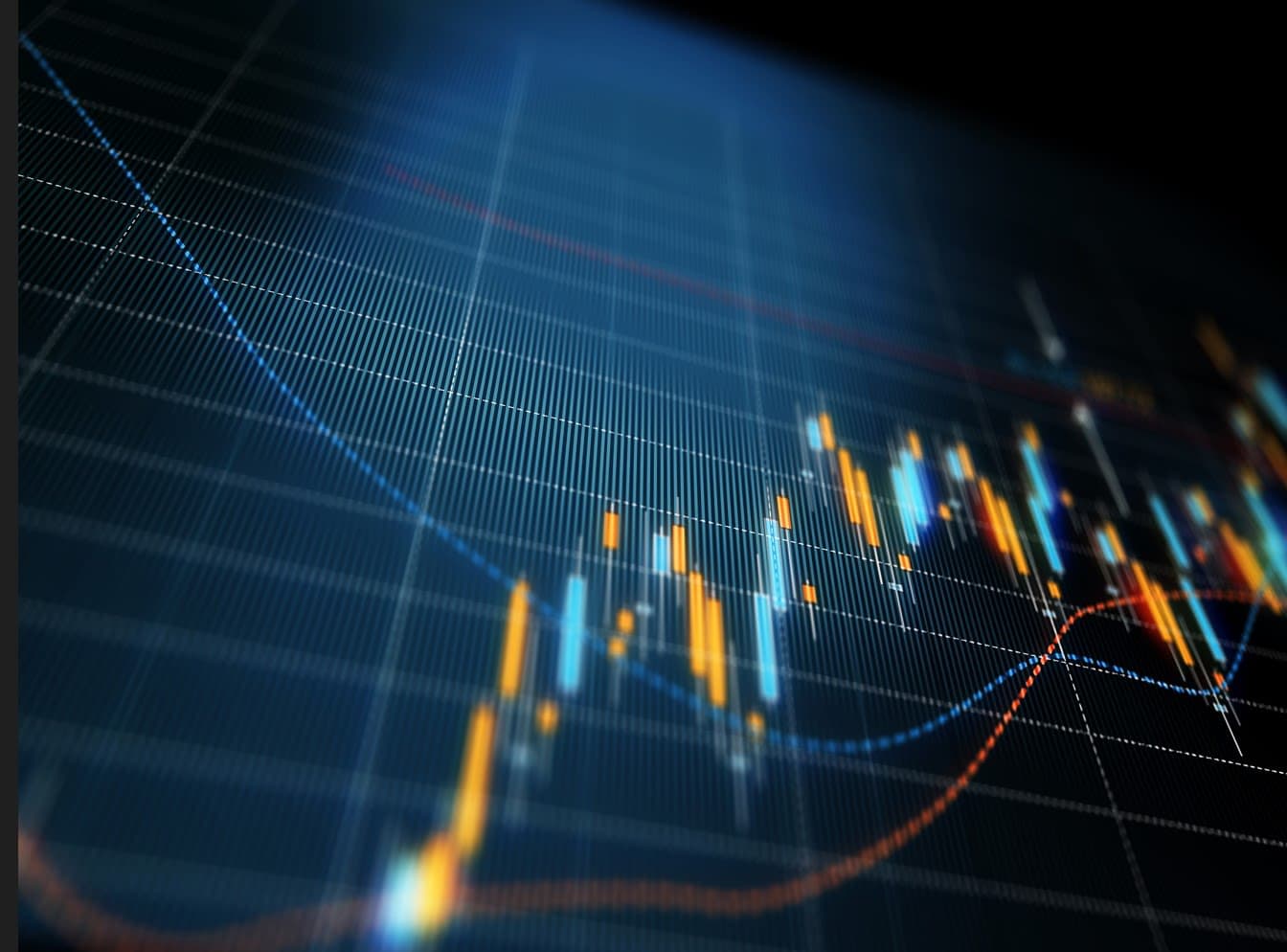
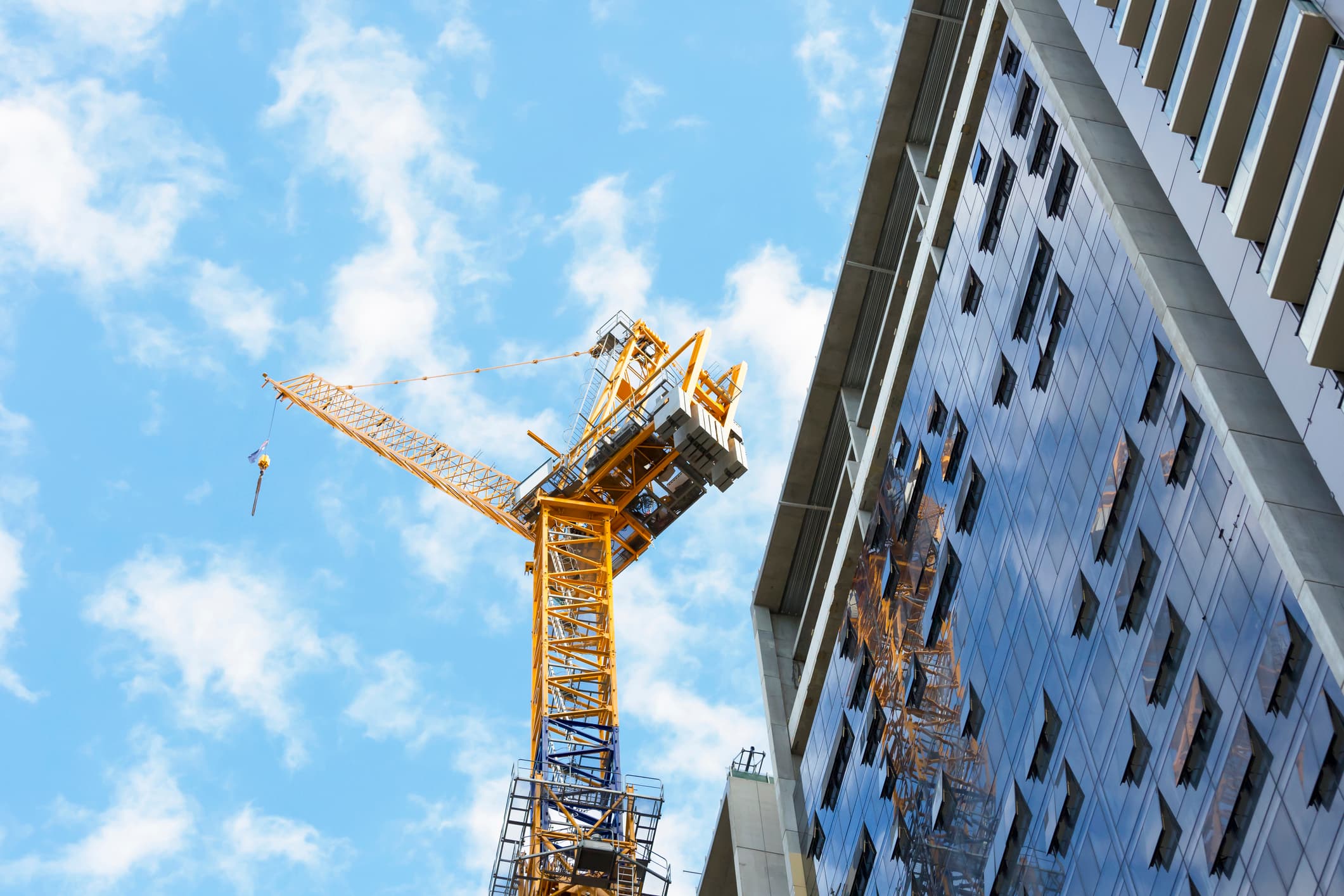
Jan 9, 2025
Building the future - Key trends shaping Australia’s construction industry in 2025
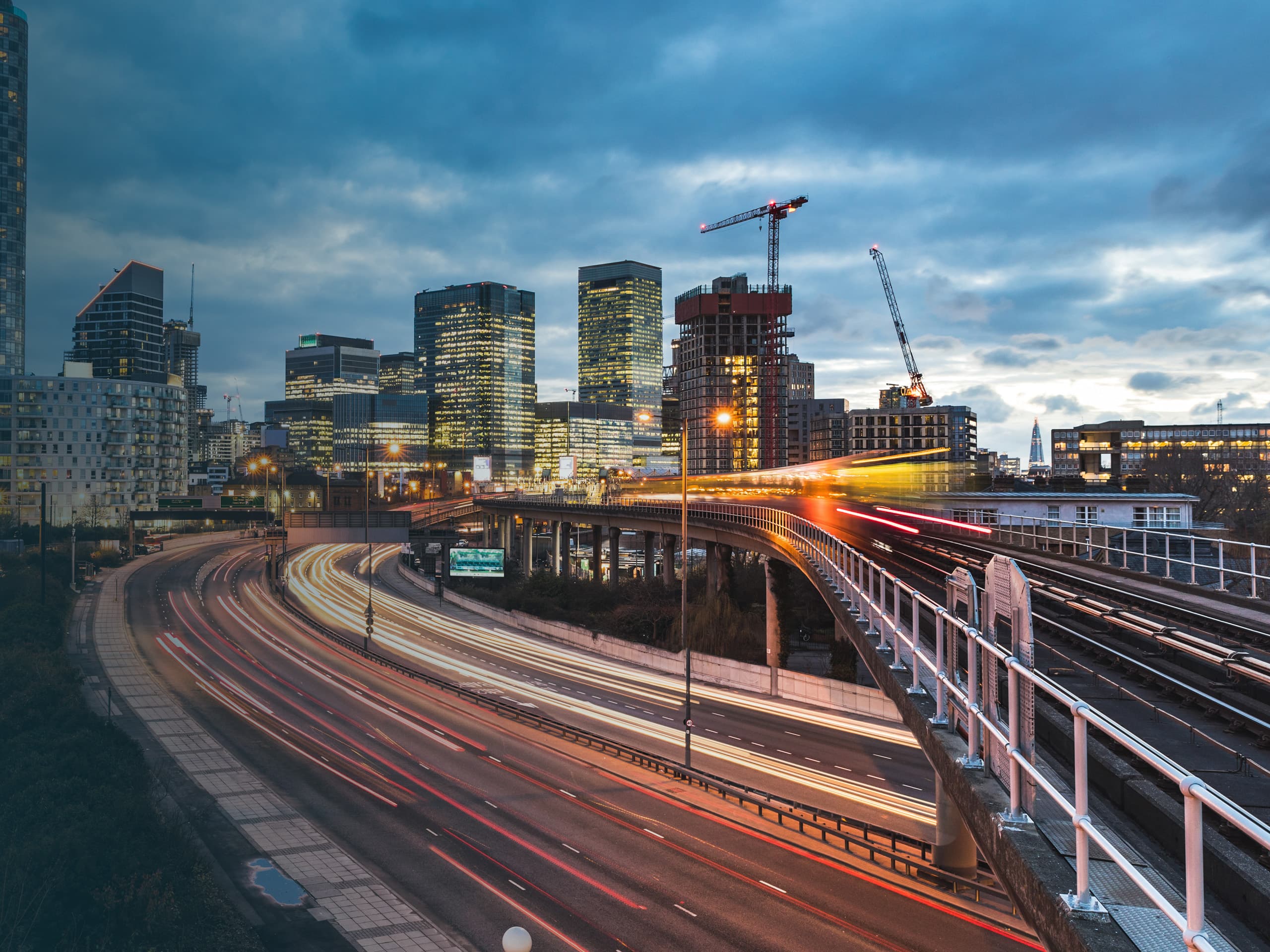