Key highlights
Australia's construction industry is navigating five notable pinch points: skills shortages, material supply, elections, equipment and weather events
Many contractors are reluctant to offer fixed contract prices, although Altus Group expects prices in Australia to stabilise in early 2023
There is an opportunity to rewrite the rules of procurement with a new 'risk, reward and responsibility matrix'
What happened
Last week, as Australia’s Reserve Bank Governor Philip Lowe announced the fifth interest rate rise in as many months, he confirmed what everyone in the construction sector knows all too well: extreme cost inflation had driven new dwelling costs up by a record 20% over the last financial year.
Amid the hyper-escalation many builders in the multi-unit residential sector have been hesitant to take on new work. But in recent weeks, participation rates are heading south in the commercial sector, too, as larger projects become just too risky to price.
It’s easy to see why. A head contractor digging a hole on a $100 million project today may not need some building materials or trade contractors until early 2024. Expecting a supplier to hold firm on a price for a year-and-a-half is not feasible after watching the last 18 months of unpredictability unfold.
So how do we make predictions in an unpredictable market? How do we make sense of cost escalation today to make the best business decisions tomorrow?
Many of the cost issues that have plagued the industry over the last two years – a perfect storm that has coalesced to create a profitless boom – continue unabated. Everything from war in Ukraine to weather woes are causing construction industry headaches.
But there are five notable pinch points for Australian construction players to unpack.
1. Skill shortages
Unemployment is at its lowest rate since 1974 – and trades can virtually name their price. Construction recorded the highest quarterly (1.4%) and annual rise (3.4%) in wages, according to the latest Wage Price Index. But these cost hikes aren’t quarantined to the construction site. Up to 25% of a project’s staffing costs are salaried administrators, and they are also asking for pay rises to offset the hit to their household budgets.
Meanwhile, debate over industrial relations reform is likely to dominate federal parliament for the remainder of the year – and cause uncertainty across the construction sector – as the Labor government looks to expand multi-employer bargaining.
2. Material supply
Buildings are constructed with the same materials all over the globe, and those materials are manufactured and fabricated from the same supply chains. Follow those supply chains along their length and they invariably land in China, where a Covid Zero strategy continues to translate into lockdowns. Earlier this month the city of Chengdu, with a population of 21 million residents, was under stay-at-home orders. The technology hub of Shenzhen, home to nearly 18 million people, is also subject to movement controls.
3. Elections
Our two biggest state governments are moving towards caretaker mode as voters in Victoria and New South Wales head to the polls in November and March, respectively. These governments may take a spending hiatus. But some projects are already in go-slow mode. The NSW Government, for instance, has just deferred $8 billion of spending to avoid cost blowouts.
4. Equipment
Sometimes pinch points emerge from unusual places. Take demand for essential pieces of infrastructure equipment, like tunnel boring machines. Victoria’s largest tunnel borers, which carved out the West Gate Tunnel, weigh around 4,000 tonnes and are 15.6 metres in diameter. The state’s longest tunnel borers, used for the Metro Tunnel, stretched to 120 metres, the same length as three E-class trams end to end. These enormous pieces of machinery are complex to construct, and there are only so many built in any one year. Australia is in the queue, alongside every other country with ambitious infrastructure agendas, to secure such machinery straight off the factory floor.
5. Weather events
After two years of record-breaking rain events, Australia is now facing a third La Niña summer, according to the Bureau of Meteorology. Wet weather has a direct impact on construction schedules, reducing time on site and cashflow. Contracts usually allow time extensions for weather, but not any cost associated with the delays. Added to this is the resources required during the rebuilding process after the damage caused in the latest round of floods. As we've explored before, the floods are adding huge loadings to projects in these regions and will drive up insurance premiums for years to come.
What will be the circuit breaker?
Five rate hikes in 2022 have lifted the cash rate to 2.35%, and the Reserve Bank has flagged two more rate rises as inflation hits 6.1%. But interest rates take time to bite and people haven’t stopped spending… yet. Australia must get inflation in check or risk the situation unfolding in the United Kingdom, where economists warn inflation could hit 18.6% in early 2023.
Altus Group expects prices in Australia to stabilise by the end of the first quarter of 2023 – but ultimately, we need to rewrite the rules of procurement.
How do we rewrite the rules?
Many contractors are now reluctant to offer fixed contract prices, given the ongoing volatility and uncertainty. Others are managing risks by charging higher than necessary prices or seeking costly and inefficient contract variations.
Some projects are already finding it more difficult to secure funding, but usually the fundamentals of these projects are borderline at best. Other projects are stepping through the tender treadmill two or three times in the hope that a bid will be cheaper, or someone will make a costing error.
None of this is ideal.
In September the NSW Government acknowledged that the rules of the road must change by publishing commercial principles for procurement. These principles include early engagement to understand the impact of escalation risks and how they could be mitigated, as well as staging projects to defer project scope where costs are uncertain or volatile, and flexible design and specification that allows for alternative materials.
These commercial principles are just that – principles – but they do recognise that risk should be allocated to the party best placed to manage that risk. It can be easy to point the finger at price escalation as budgets blow out, but there are foreseeable risks that can managed. Just one obvious example is to reconsider whether the construction contractor, skilled at pouring concrete, is also the best party to carry out community engagement activities.
Risks cannot be pushed down the line without consequences. When a subcontractor falls over, it becomes the builder’s problem by default – but when the burden becomes too big, that builder is also at risk. This makes it everyone’s responsibility to take an active role in managing escalation, and working together to rest the risk, reward and responsibility matrix.
Author
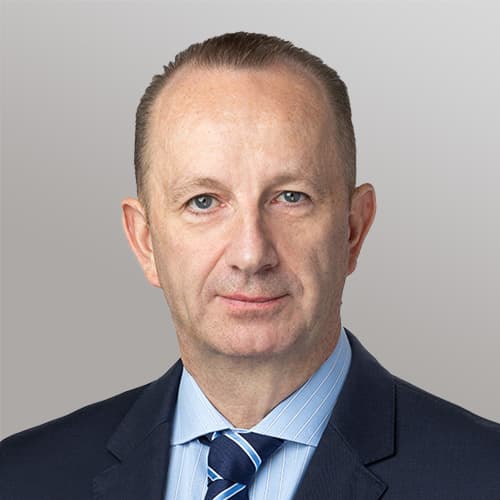
Niall McSweeney
President, Cost and Project Management, Asia Pacific
Author
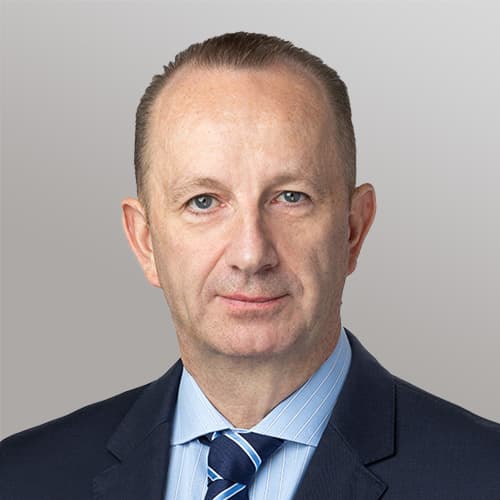
Niall McSweeney
President, Cost and Project Management, Asia Pacific