Between now and 2050, around half of all the emissions generated by new construction will be locked in before anyone steps through the front doors of a building, drives on a road or crosses a bridge. These emissions can only be addressed once – upfront. As Altus Group’s Associate Director Zheng-Yang Ong notes: "We are making design decisions today that will have consequences for decades to come”.
So, how do we calculate the carbon emissions that are generated upfront?
What is embodied carbon and why does it matter?
According to the World Green Building Council, around 40% of global carbon emissions come from buildings, 29% from building operations and the other 11% created ‘upfront’ during the manufacture of materials and construction. Last year, 10% of the world’s energy was generated by solar and wind. As more buildings are powered by 100% renewables, this will drive attention towards the next biggest source of emissions – those generated upfront. By 2050, as the world’s population approaches 10 billion, our global building stock is expected to double its current size.
According to the World Green Building Council, carbon emissions released before the built asset is used will be responsible for half of the entire carbon footprint of new construction. The term ‘upfront carbon’ is often used interchangeably with ‘embodied carbon’, but they are slightly different terms. Upfront carbon refers to the emissions generated in the first two phases of a building’s life, during product manufacture and construction.
During the product phase, carbon is emitted as raw materials are extracted and transported, on the factory floor, and as products are shipped around the world. Steel, cement and aluminium each produce between 7% and 9% of global emissions, but there are hundreds of building components that add up to a large carbon footprint. At the construction stage, around 5.5% of the industry’s emissions are generated from powering machinery and equipment. Think about all those fossil fuels burnt to power cranes, trucks and tools.
But ‘embodied carbon’ also covers the emissions generated during a building’s repair and refurbishment, as well as the end-of-life stage of demolition and disposal. As governments set net zero targets and consumers demand climate action, investors and building owners are beginning to ask themselves a simple question: Would a price on embodied carbon influence the value of my asset?
How do we measure carbon content?
Better management always starts with measurement – but measuring embodied carbon is extremely complex. Where do we start? It is the job of a quantity surveyor to answer this question. “A quantity surveyor understands how to calculate quantities of materials and can apply that knowledge to calculate the quantity of carbon content in each material,” says Niall McSweeney, Altus Group President for Cost & Project Management, Asia Pacific.
“A quantity surveyor can also provide insight into the carbon footprint of a project across its full cycle.” Carbon calculations can’t be sketched out on the back of an envelope. Some of the questions that a quantity surveyor will ask and answer include…
Materials: Is each material choice evaluated against its true lifecycle cost? Is each product backed by an independently verified Environmental Product Declaration? Will the product be tested by a material scientist to verify the carbon content?
Transport: How far must the product travel from the factory floor to the construction site? When weighing up the carbon and financial cost of an imported product, does a local product present a stronger business case?
Equipment: Will on-site construction equipment and machinery be powered by fossil fuels? What equipment can be replaced with 100% electric options?
Project specifics: What impact will the design decisions – from the structural type to the number of floors – have on the carbon content of the project?
Project boundary: How much of a building will we consider? Will we stop at construction? Or will we consider refurbishment over a 50-year lifespan and demolition and disposal at the end of a building’s life?
Ancillary costs: What is the carbon impact of the roughly 30% of a project’s cost that covers everything from site offices to support staff? How will we measure and manage those costs?
Waste: Can we adopt construction technologies and techniques to minimise waste on site?
Optimisation: How can we design the building to repurpose, renovate and reuse existing elements to optimise the embodied carbon that is already there?
Future focus: How will the asset be deconstructed at the end of its life? Is the building designed for disassembly to support future reuse and recycling?
It makes sense to eliminate any unnecessary costs upfront – and upfront carbon emissions can be reduced by 20-40% with good design decisions and careful selection of materials. But that still leaves up to 80% of a building’s upfront emissions locked in. By purchasing carbon offsets, a company then compensates for the carbon emitted by investing in projects that plant tree, invest in energy efficiency or restore biodiversity.
Can carbon become a new measure of value?
“Ultimately, the building with the lowest carbon impact is the one that never gets built,” Niall notes. “The next best solution is to ensure each building is highly-efficient and performs at its peak.” As a new value engineering opportunity emerges – one that transcends the traditional dimensions of cost, time and quality – a quantity surveyor must be involved from the earliest planning phase, adds Yang.
“A quantity surveyor lays the ‘track’ and finds the efficiencies. As we weigh up the costs of embodied carbon, eliminating upfront emissions can become a new lever to adjust project design and uncover new value.”
Authors
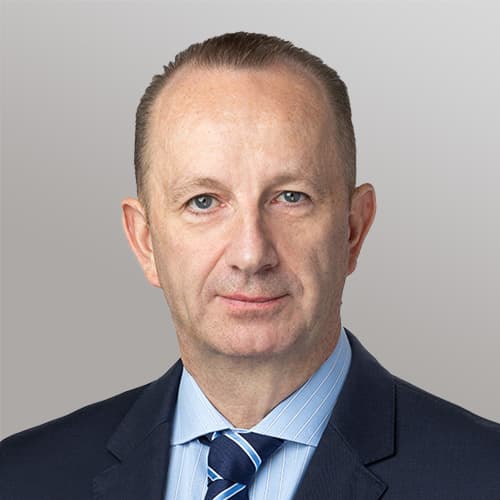
Niall McSweeney
Head of Development Advisory, Asia-Pacific
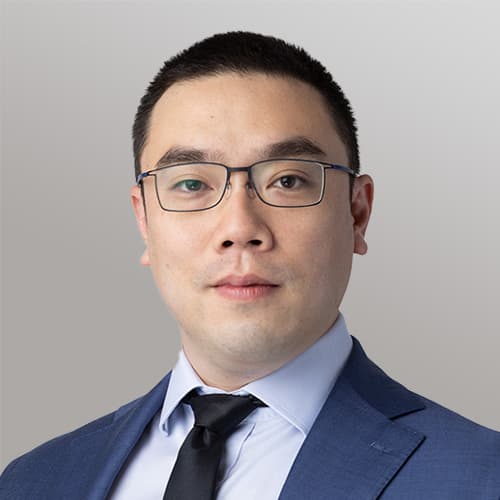
Yang Ong
Associate Director
Authors
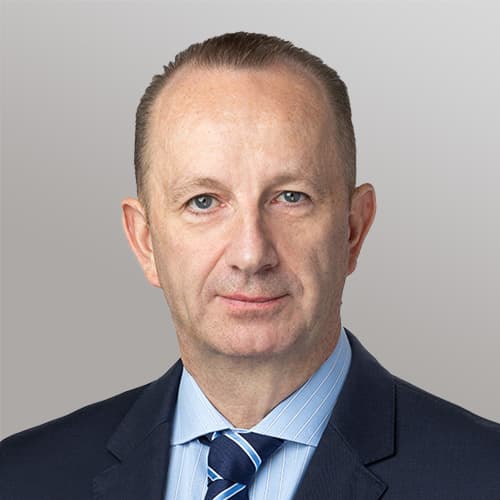
Niall McSweeney
Head of Development Advisory, Asia-Pacific
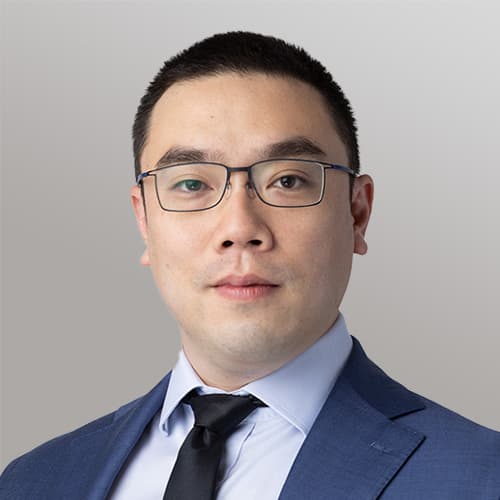
Yang Ong
Associate Director
Resources
Latest insights
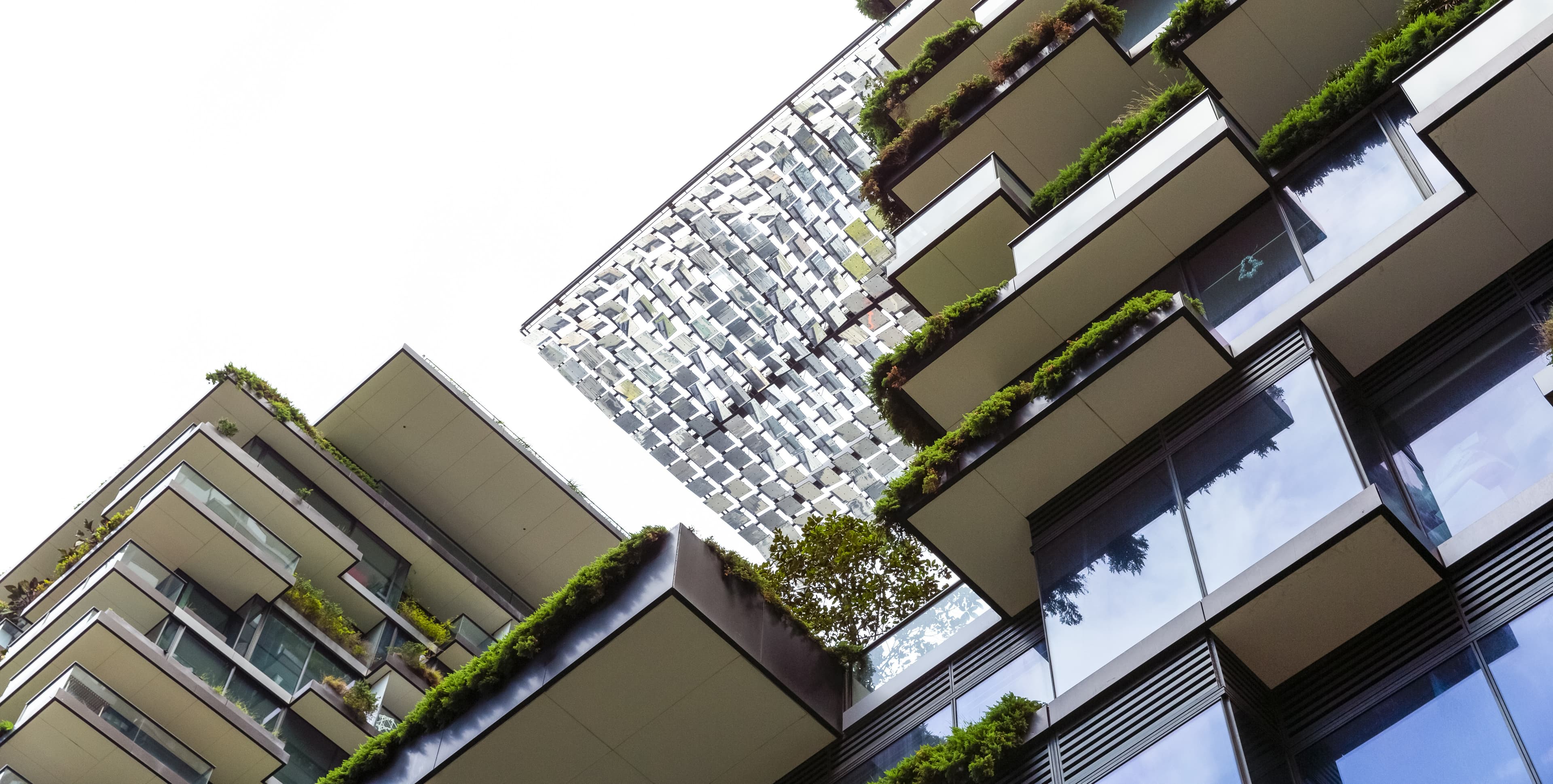
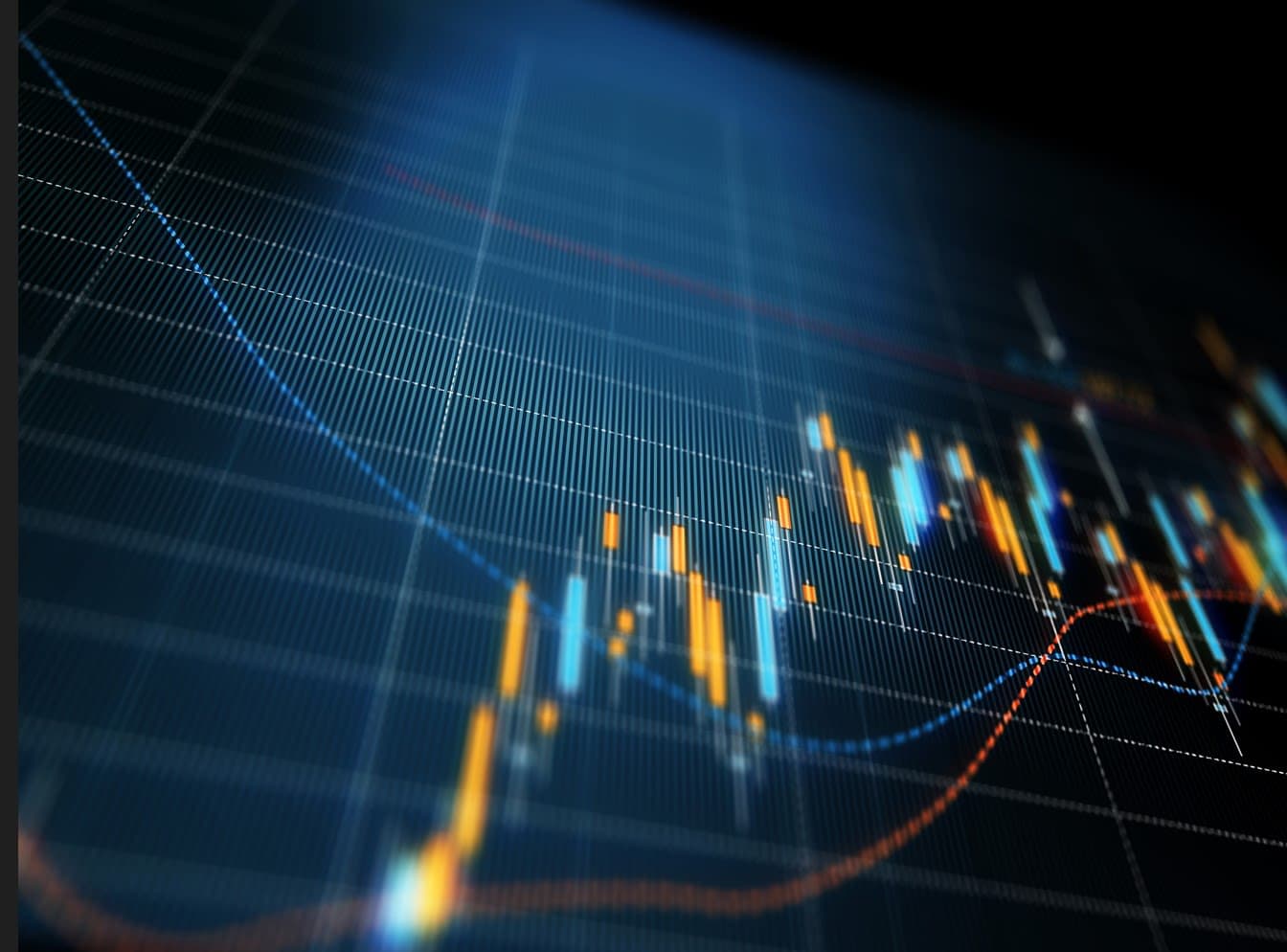
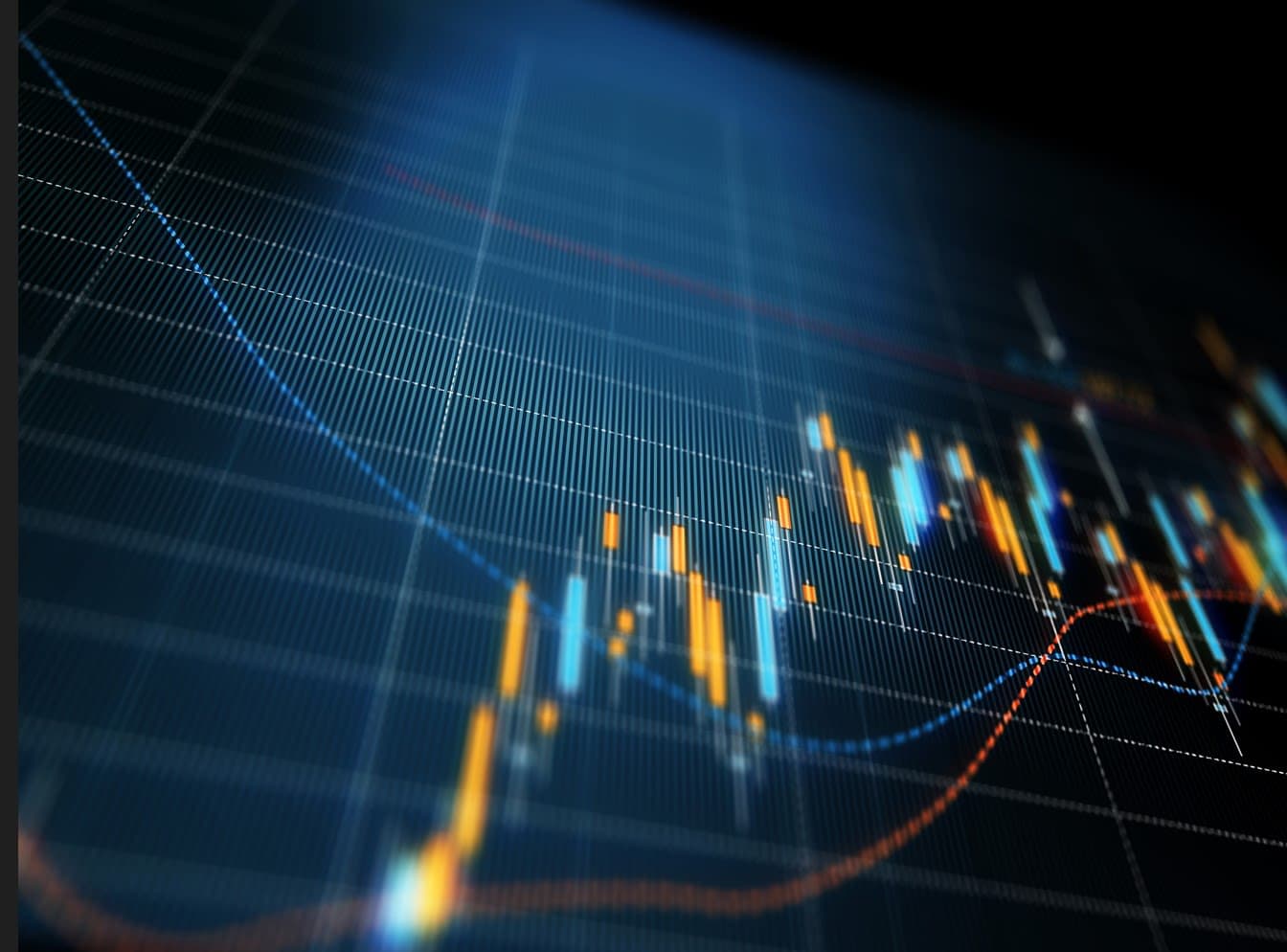
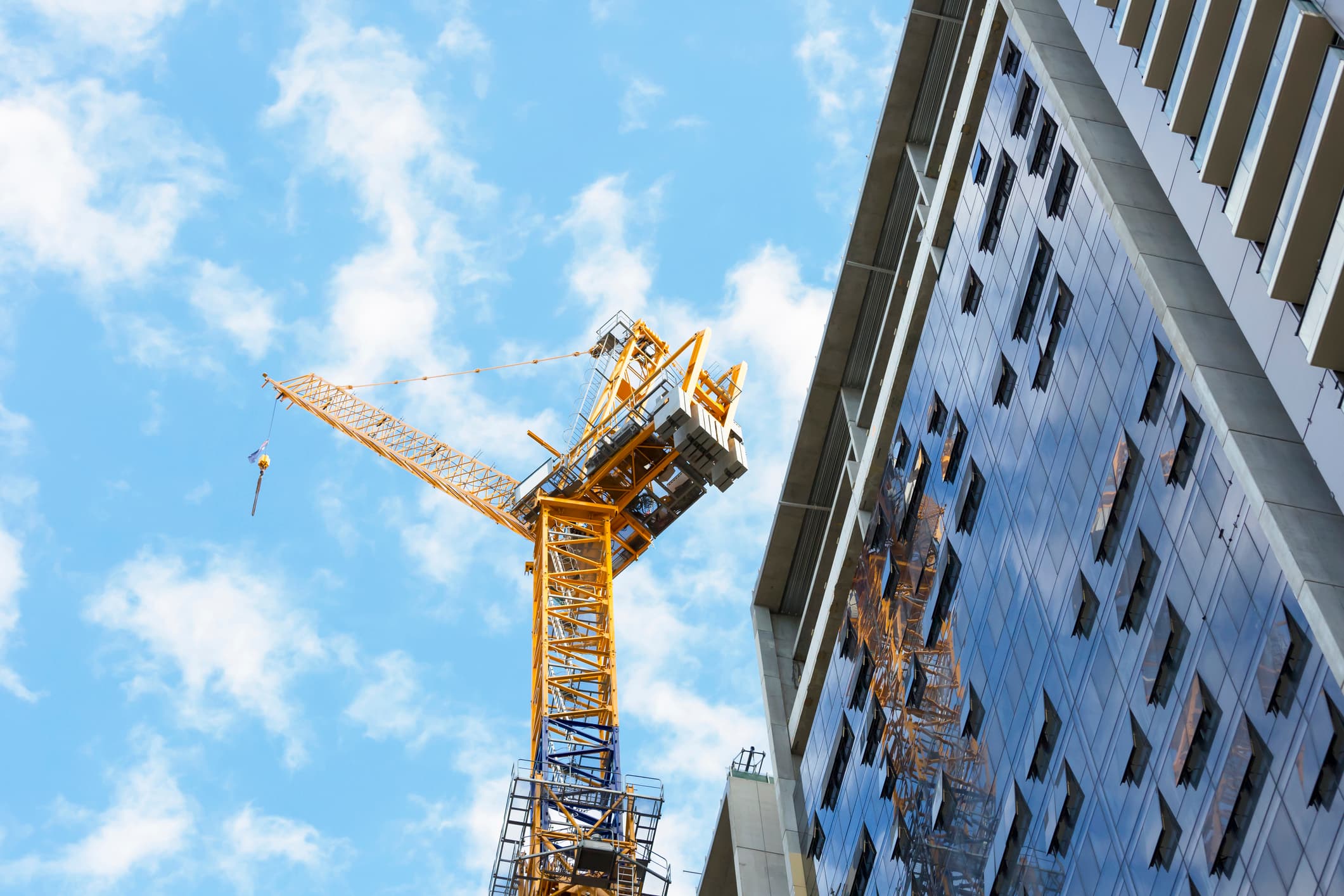
Jan 9, 2025
Building the future - Key trends shaping Australia’s construction industry in 2025
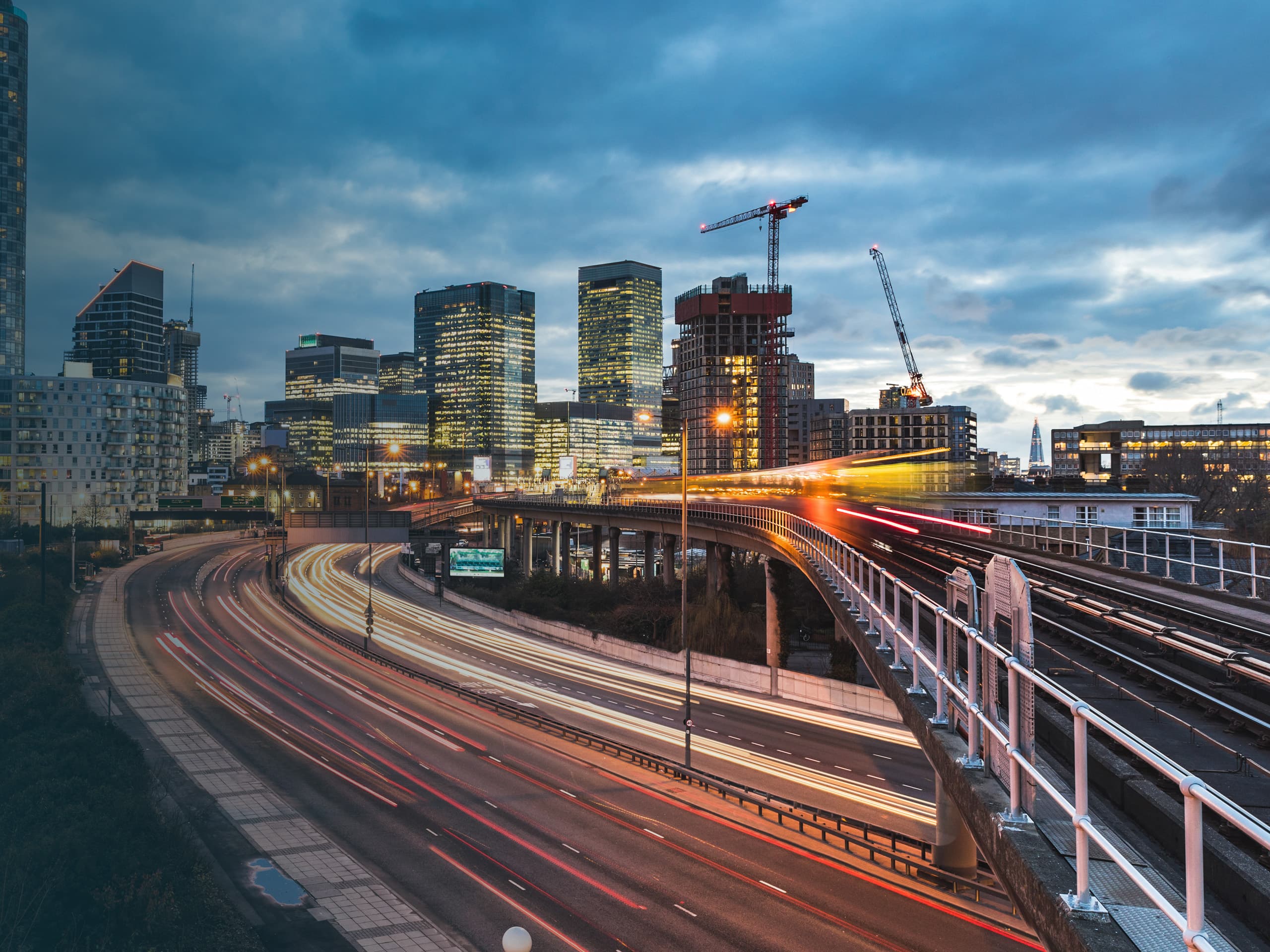