Key highlights
Rework – which crimps construction profit margins, erodes quality and reduces confidence in the trustworthiness of buildings – also comes at a high carbon cost.
Up to 80% of a building’s total carbon footprint can be locked away in building materials.
As designers and developers look for ways to reduce upfront or embodied carbon emissions, reducing rework is a quick win hidden in plain sight.
As the construction industry begins to count the cost of embodied carbon, rework is a glaringly obvious but overlooked source of emissions.
“Not good enough. Do it again.” It’s a phrase that no one wants to hear. Rework plagues every part of the construction industry – stealing hours, days or even months from projects, jeopardising budgets and timelines and the reputation of businesses.
The general industry consensus is around 5% of a construction budget is spent on rework. While this can vary depending on a project’s size, complexity and location, the costs of rework can often be eyewatering. One 2018 Australian study from Bond University, which examined 19,605 rework events from 346 construction projects, estimated the costs at 34% of budget. This reduced the mean yearly profit by a staggering 28%. As project managers try to claw back time or cut corners, quality and site safety can be casualties.
NSW Building Commissioner David Chandler AO is on a mission to lift the quality of building and consumer confidence in what he calls “trustworthy buildings”. The NSW Building Commission has introduced the Design and Building Practitioners Act to reverse what Chandler calls a “construction confidence crisis”. New South Wales now has audits of occupational certificates and mandatory minimum design documentation – but the problem of defects is widespread.
One 2021 survey of 1,400-plus strata managers in New South Wales recorded serious defects in 39% of residential, or Class 2, buildings. Nearly a quarter (23%) of those defects are related to waterproofing, another 14% to fire safety systems and 9% to structural. Shortcuts taken during design and installation can come with a hefty rework bill. The report found the average cost for owners’ corporations to rectify those defects was $332,000 per building.
Rework and re-emit-tances
Rework also comes at a huge environmental cost. The aspirations of a green design can be severely diminished by rework when large quantities of materials are discarded to “do over”. While it’s hard to estimate how much waste is generated through rework, we know around 12.7 million tonnes of construction waste is sent to landfills each year.
How much carbon was generated to manufacture those materials that languish in landfill? We know as much as 80% of a building’s total carbon footprint comes from the materials used during construction.
Altus Group is working with clients around the world to calculate the costs of embodied carbon emissions on construction projects (and you can read more in our article on Counting the cost upfront).
This includes the carbon generated as raw materials are grown, extracted and transported, as building products are manufactured on the factory floor and then shipped around the world, and as materials are transported and installed onsite.
Steel, cement and aluminium each produce between 7% and 9% of global emissions, for instance, but there are many building materials, from plasterboard to tiles, that are regularly torn out and thrown away thanks to rework.
Then there’s the carbon cost of project delays. More days on-site mean more emissions generated during the transportation, storage and handling of materials.
Sustainable solutions
The reasons for rework are multi-faceted – from design errors to communication breakdowns to poor workmanship. And a multi-faceted problem demands many solutions.
Innovative construction methods that cut down the time and intensity of onsite construction are a good place to start. Prefabrication, with its precise manufacture on the factory floor, produces less waste and fewer emissions offsite, and also reduces waste materials, construction traffic and associated emissions onsite. (Further reading on prefabrication can be found in our modular guide.)
Digital technologies, especially digital twins, can help the construction industry to streamline collaboration and better visualise projects to identify potential clashes and problem spots.
Education – like the NSW Building Commission’s multi-disciplinary design training – can also encourage more holistic thinking. Quality control processes are more successful when each player in the construction value chain understands their role in delivering a quality product.
Finally, a standard method of measurement for embodied carbon will elevate the issue of rework. A project is underway, led by the National Australian Built Environment Rating System, in collaboration with the Australian Institute of Quantity Surveyors and more than 100 other industry players, to set industry-agreed benchmarks for embodied carbon. With a national standard to help the construction industry measure and monitor embodied emissions, the costs of rework will become too big to ignore.
Author
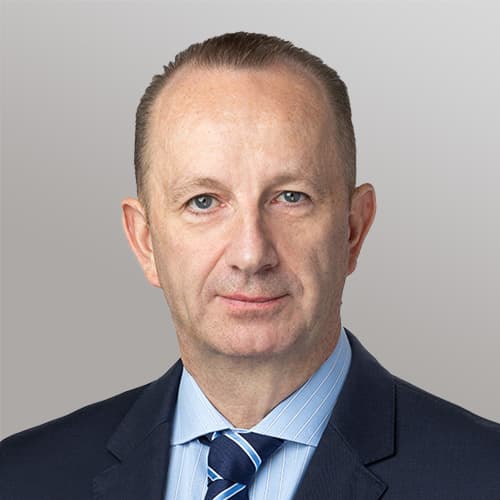
Niall McSweeney
Head of Development Advisory, Asia-Pacific
Author
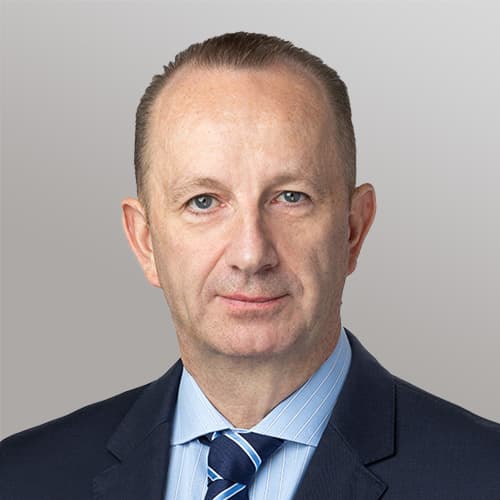
Niall McSweeney
Head of Development Advisory, Asia-Pacific
Resources
Latest insights
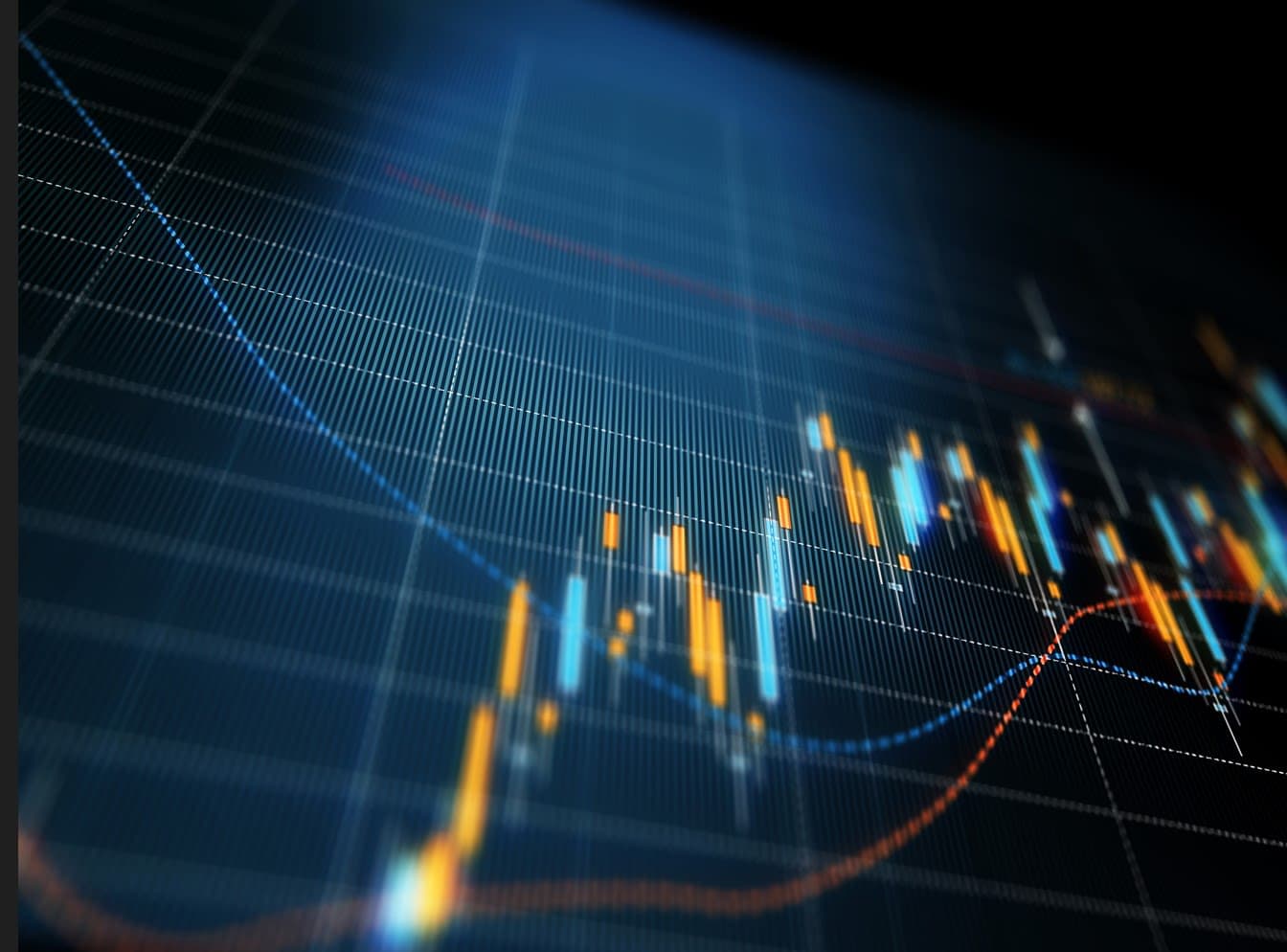
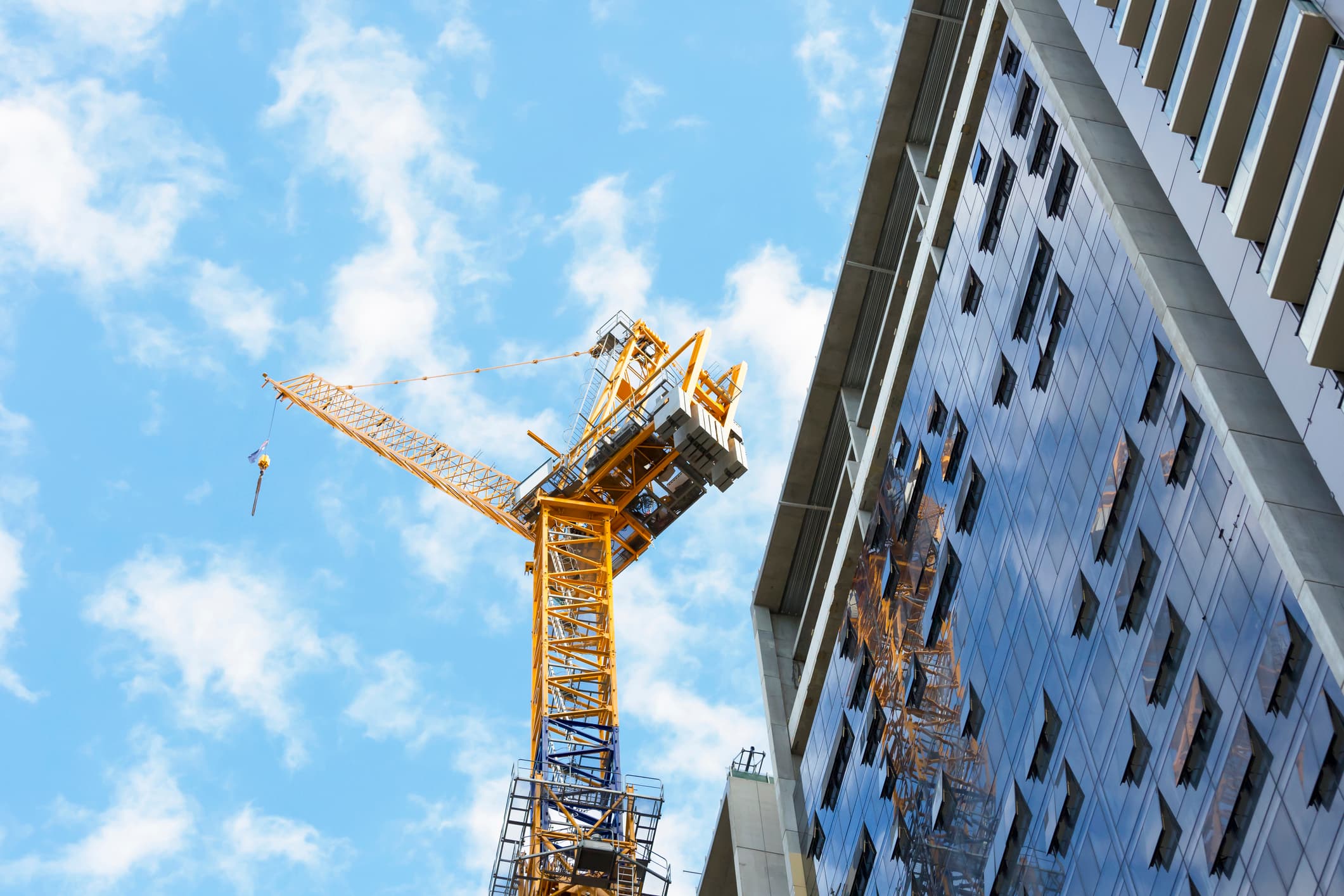
Jan 9, 2025
Building the future - Key trends shaping Australia’s construction industry in 2025
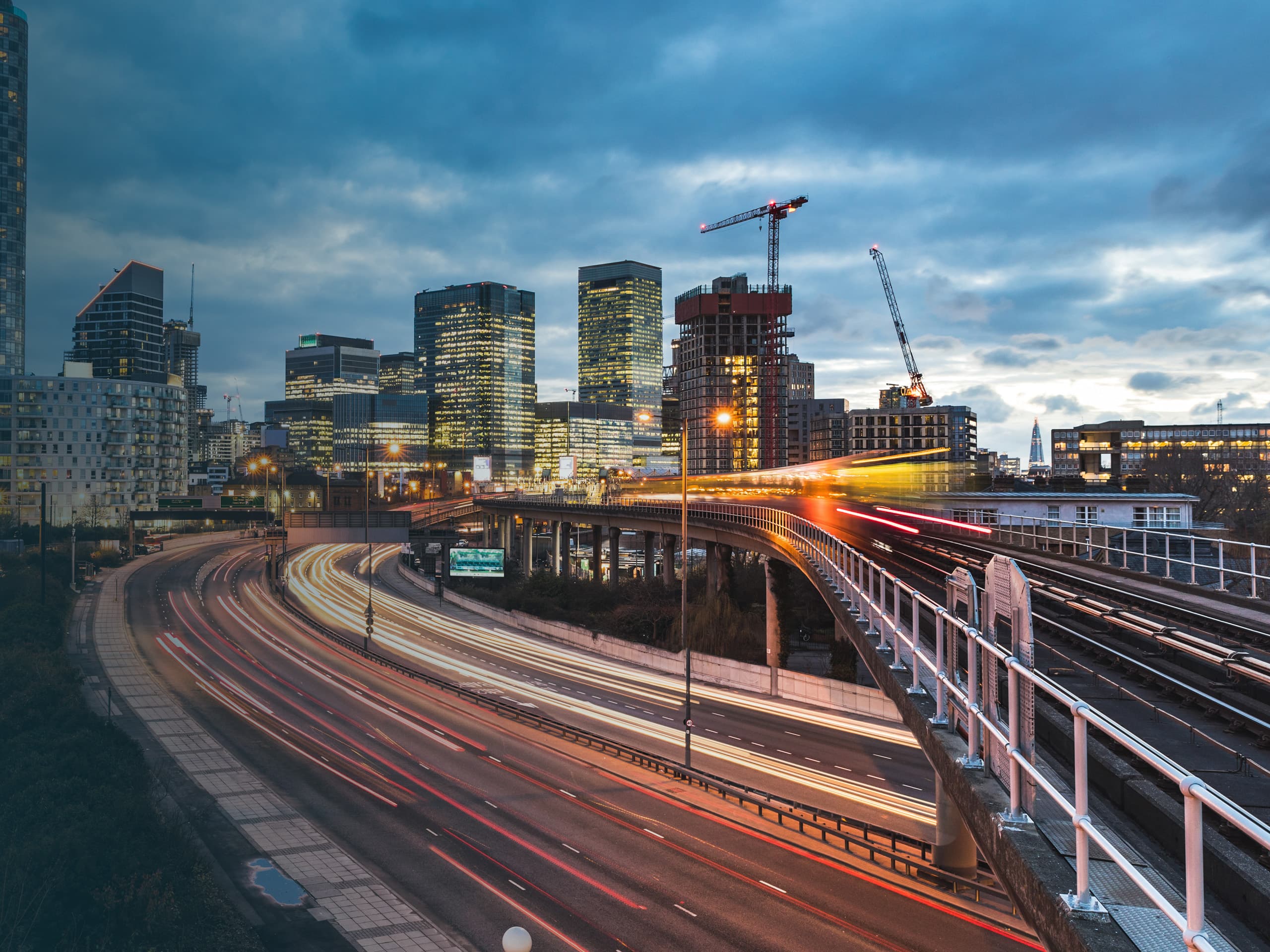
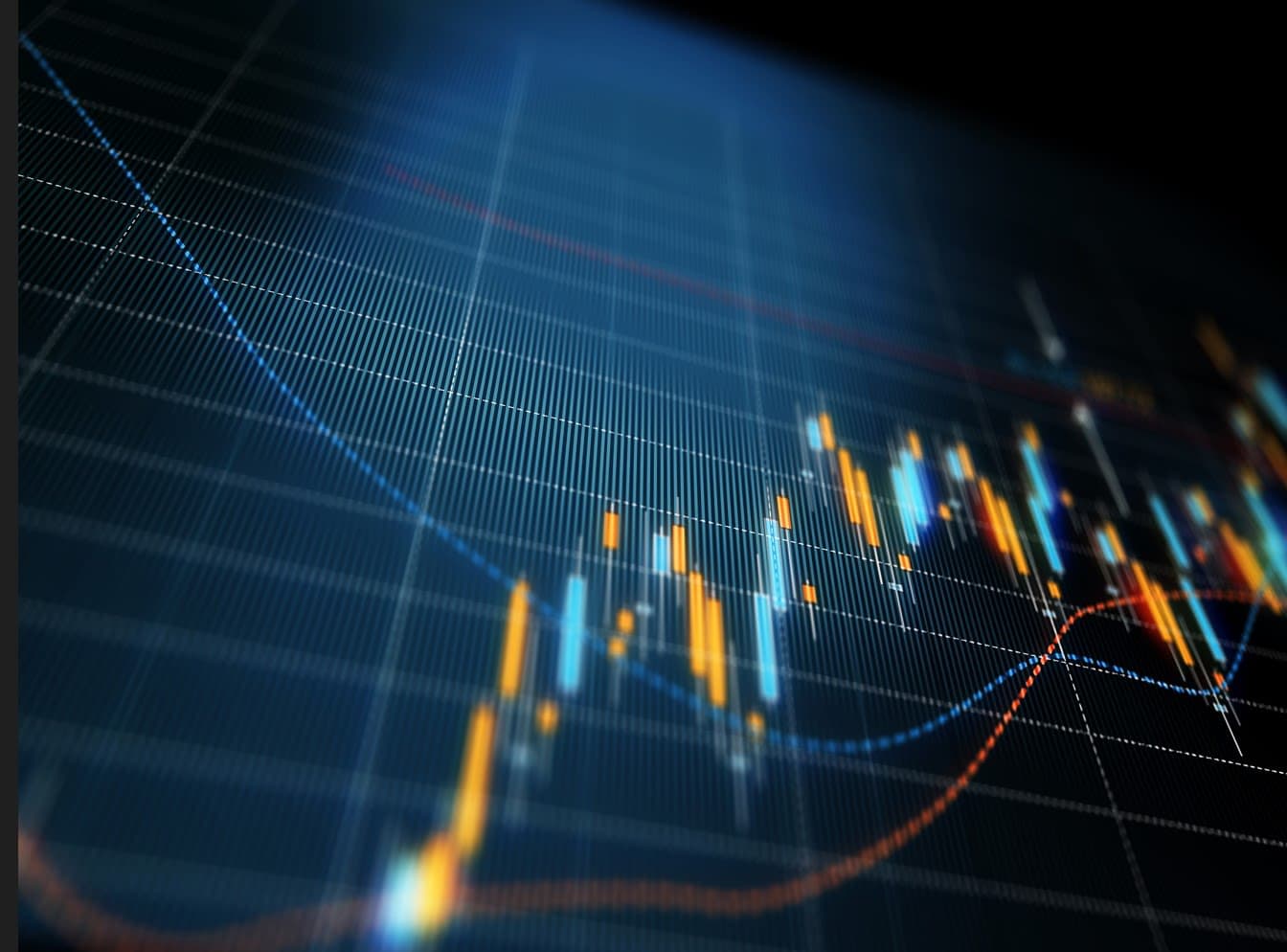
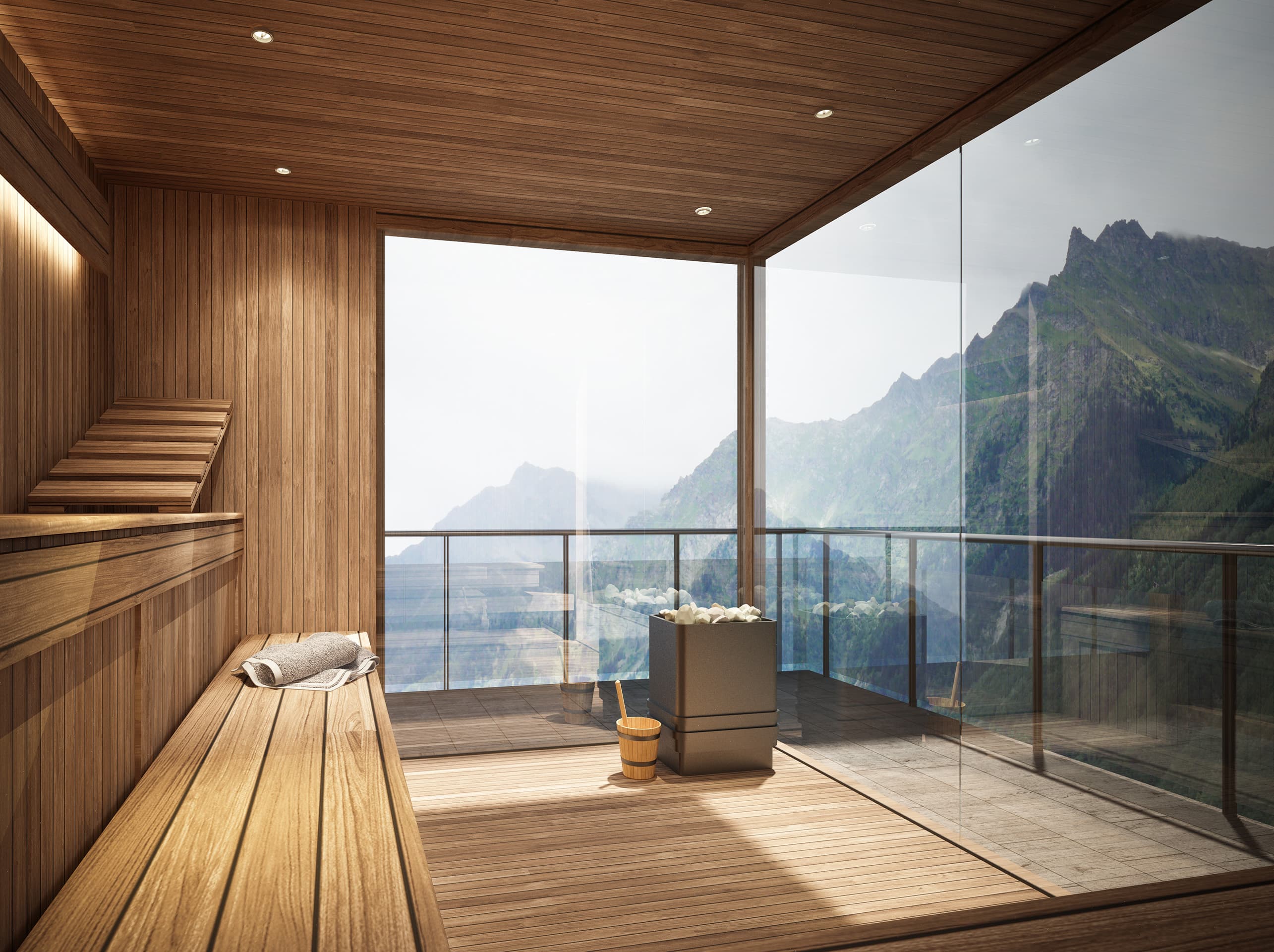
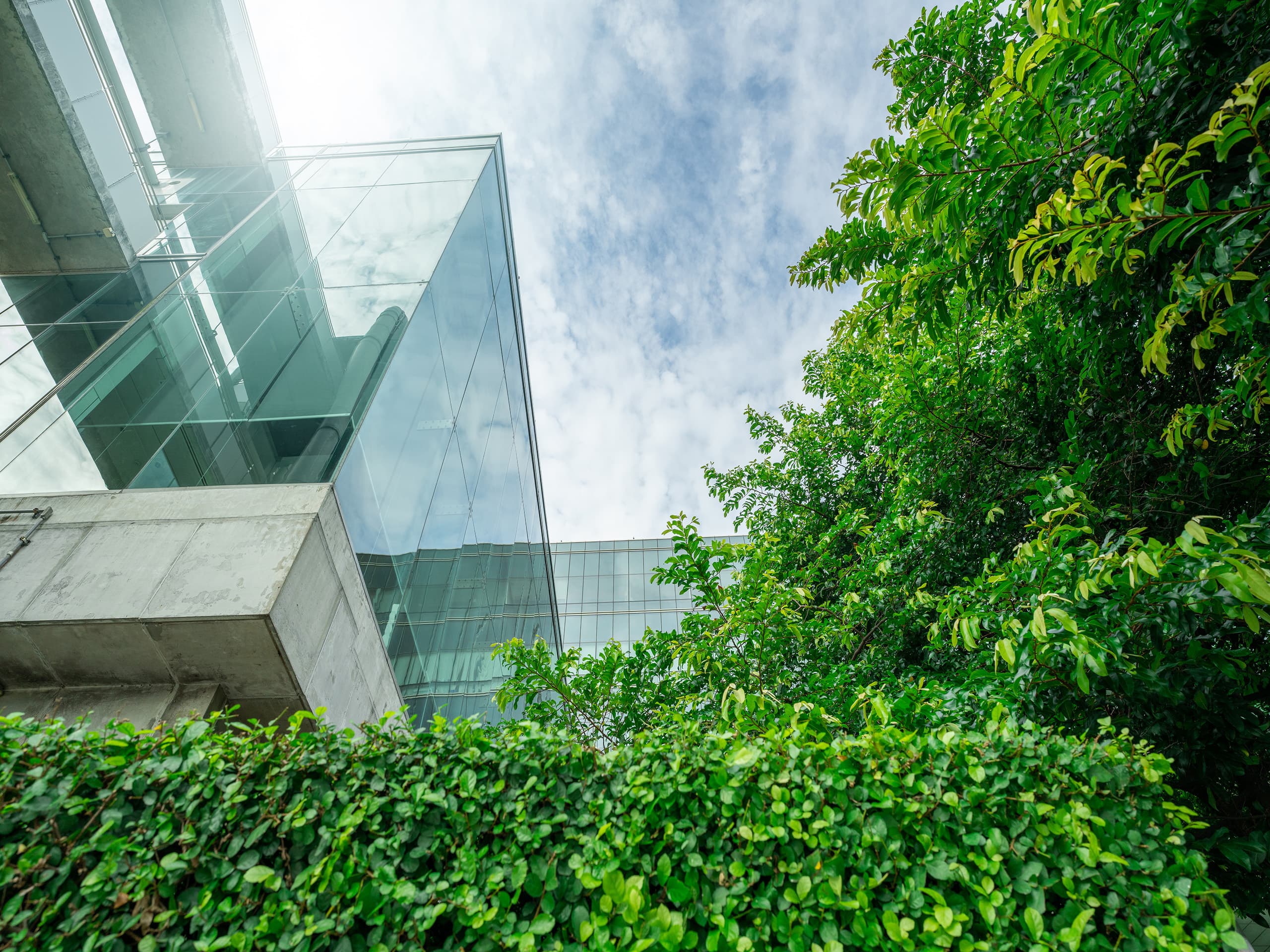