Key highlights
Same-day delivery, shrinking land availability and sustainability are all driving developers towards multi-level industrial, logistics and warehousing projects
When thoughtfully designed and delivered, these buildings can be stitched into the fabric of our cities – but eye-catching facades, wellness facilities and community amenities come at a cost
Feasibility studies for multi-level projects aren’t as easy as multiplying single-storey benchmarks and several flawed assumptions can prevent multi-storey industrial projects from getting off the ground
The rise of multi-storey warehousing
The industrial sector emerged as a big winner from the pandemic, fuelled by the e-commerce juggernaut – demand for data, fast delivery and the freshest food and pharmaceuticals. Now, more than ever, the need for speed is transforming supply chains, and driving developers towards multi-level industrial.
Around 10% of Australian purchases are now made online, and some analysts estimate we will need 1.8 million extra square metres of industrial and logistics space to accommodate the next five years of e-commerce growth.
Australia also has the lowest industrial vacancy rate in Asia Pacific, with a national average of 0.6% for prime space. In Sydney, the nation’s tightest and most expensive industrial rental market, there is limited serviced industrial land available, and the vacancy rate is hovering at 0.3%.
Research shows around a quarter of customers abandon online shopping carts because estimated delivery times are too slow. To this effect, Australia Post has just launched its ultra-fast delivery service, with ‘next day’ delivery now possible in most capital cities. But customers in many markets, notably China, now expect a delivery at their door within 30-minutes. That’s where the trendline is pointing.
Facilities close to the customer can deliver significant savings, as up to 50% of supply chain costs are correlated with transport (compared to up to 10% on real estate).
But the carbon savings could be even more significant. Around 18% of Australia’s emissions come from transport, and a modern facility in the right location can make big inroads into a company’s emissions footprint. MIT’s Real Estate Innovation Lab has found transportation emissions from an urban fulfilment centre are around half that of an out-of-town hub.
Tall orders are in town
All these drivers are propelling property developers towards multi-level warehousing – but how tall are we talking? Multi-storey facilities are typically three or four levels, although Hong Kong’s GrandTech Centre soars to 22 storeys.
In April, ESR completed the world’s largest multi-storey distribution centre in Tokyo, with a gross floor area of 349,000 square metres (m2) across nine storeys (and on just 77,725 m2 of land near Haneda airport). Closer to home, ESR recently acquired a 4.8-hectare site in South Sydney, with plans to develop a $300 million multi-storey warehouse facility.
The story of Sydney, given its tight industrial vacancy rate, is particularly interesting. CBRE expects at least six multi-storey facilities will be built in Sydney over the next two years, and says around 15% of total new industrial floorspace delivered in the city between now and 2027 will be multi-storey.
Goodman Group has invested $700 million in two inner-city Sydney sites and promises to introduce “a new building typology”. The first is a 30-metre-high, three-level facility in St Peters, which will hold around 47,000 m2 of warehousing space. Semi-trailers up to 20 metres will access the levels via a 55-metre diameter spiral ramp. The second is a two-level project that is 20,000 square metres in Alexandria. Designed by acclaimed architect FJMT, the building, Goodman Group says, “balances raw industrial style with refined premium aesthetic”. The building boasts state-of-the-art, end-of-trip facilities, is adjacent to a park, and is targeting a 5-star ‘Green Star’ rating. These are all features that are attractive to workers and will create an appealing aesthetic and amenity within the local neighbourhood.
If the future multi-storey facility is much more than a grey box, the obvious question is: how much does it cost?
Higher aspirations, higher costs
The height of an industrial facility might stack up, but does the feasibility? Industrial developers must also consider that moving to multi-storey isn’t simply a matter of multiplying a single storey m2 rate. With current volatility in the market, Altus Group is seeing varied tender returns for multi-level industrial units; however, these are all significantly higher than typical, single-storey projects that may have been considered for benchmarking in the past, but don't apply to this form of construction. Moreover, low supply in cities like Sydney is contributing to higher rental rates and, therefore, may impact the feasibility of projects and, subsequently, the construction supply in the Sydney area.
The structure, depending on the ground conditions, may require stronger columns and a thicker slab. Extra floors require more mechanical services and space for plant and equipment. Reticulation of services is more complex and costly.
A building’s façade accounts for around 30% of the cost of a commercial project, and we are beginning to see designs for multi-storey industrial buildings which mirror the quality of commercial offices. An attractive façade can enhance the local neighbourhood, but it can also come at a significant cost. Preliminaries are also much higher on multi-storey – think 20%, rather than 10%. Then there’s additional costs for cranes and scaffolding, labour, site and traffic management, staging requirements and safety. These factors, as you can surely guess, contribute to higher construction costs.
The bottom line? The industrial sector has benchmarked buildings based on single storey construction – and using these numbers for feasibilities could end up in failure. That doesn’t mean we shouldn’t be moving to multi-storey industrial. It just means understanding the implications. The higher the building, the bigger the budget.
Author
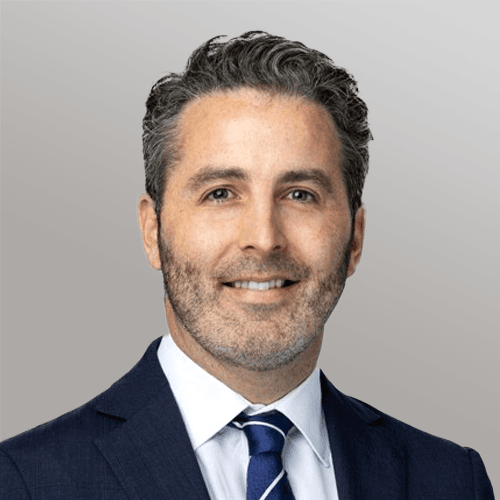
Barry McBeth
Director, Cost Management
Author
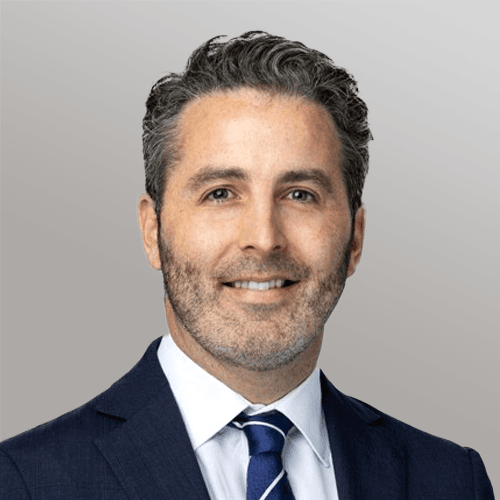
Barry McBeth
Director, Cost Management
Resources
Latest insights
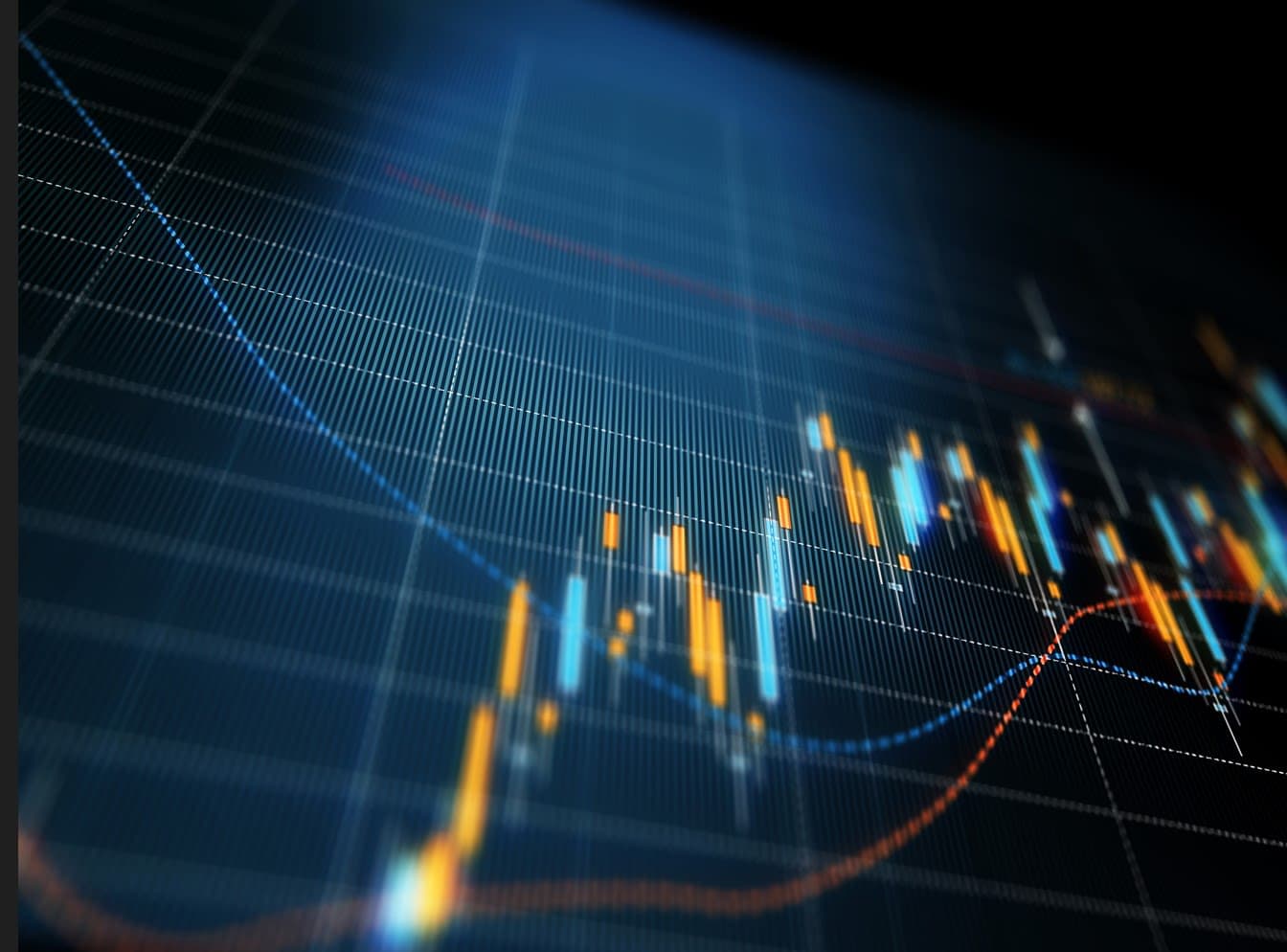
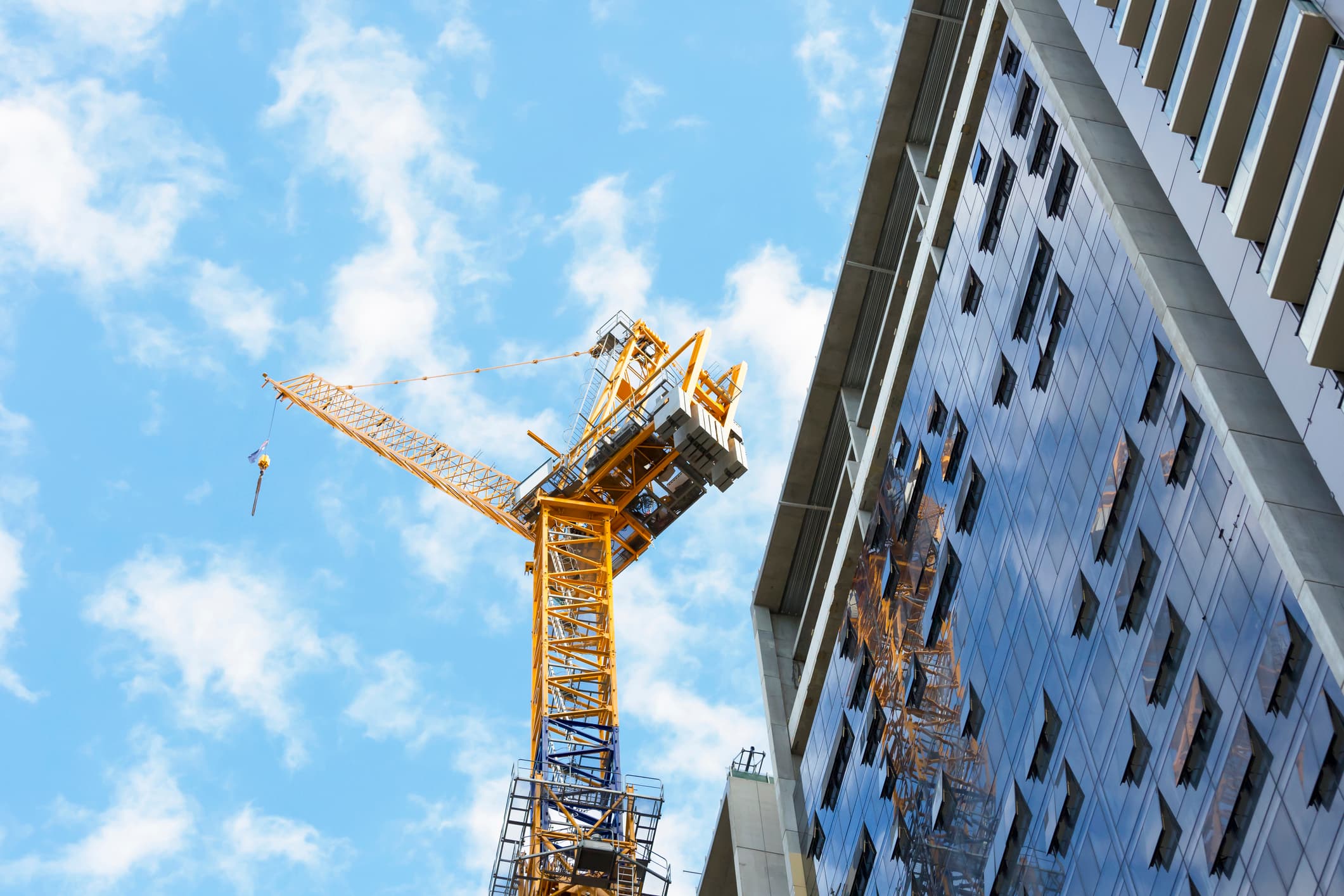
Jan 9, 2025
Building the future - Key trends shaping Australia’s construction industry in 2025
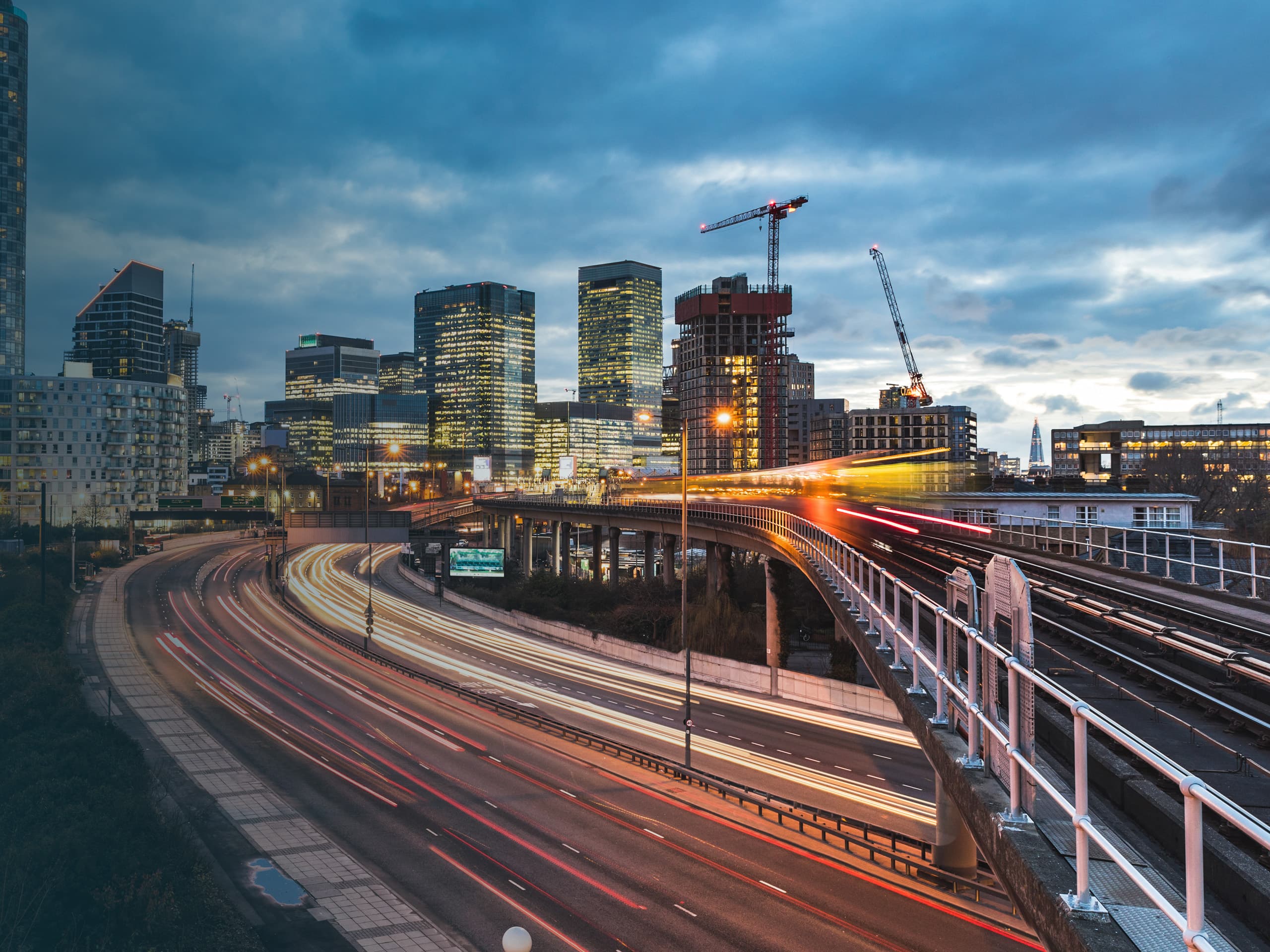
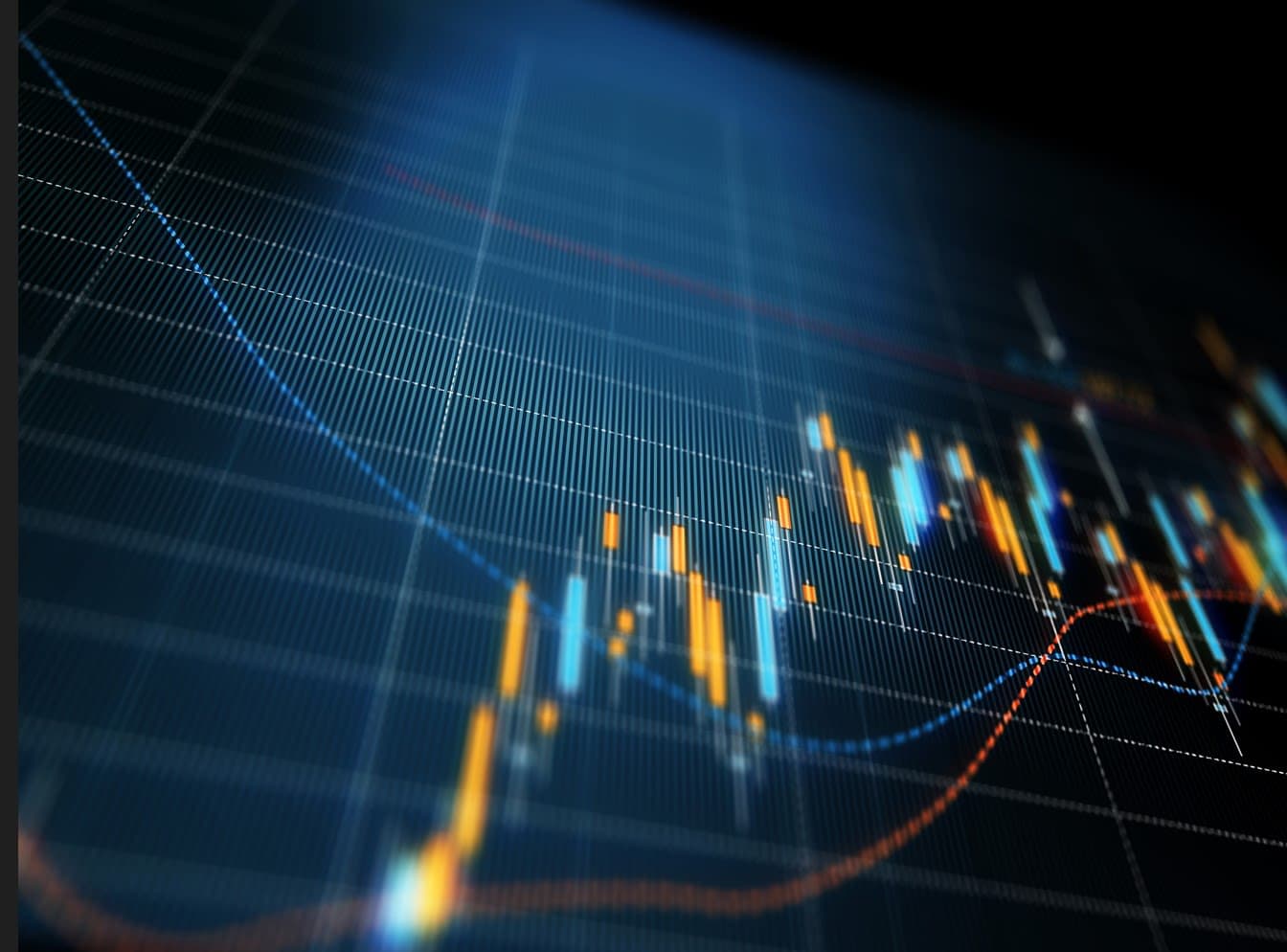
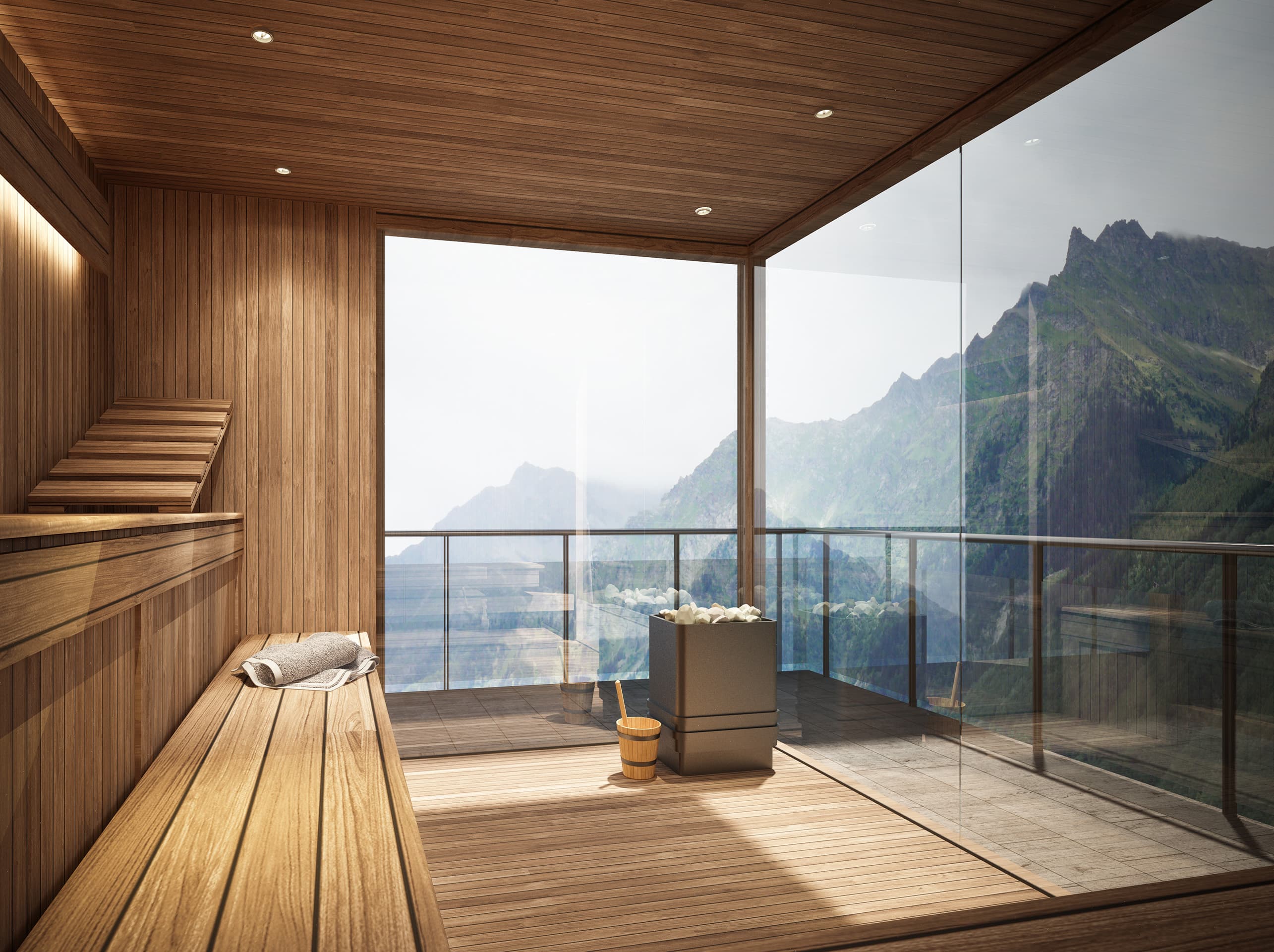