Points saillants
Les plus grandes entreprises de construction et propriétaires d'actifs d'Australie ont fixé des objectifs de zéro émission nette, mais ceux-ci seront impossibles à atteindre sans porter notre attention sur les émissions de carbone incorporées.
Une méthode standard de mesure des émissions de carbone incorporé est la première étape vers une meilleure gestion
La collaboration entre les métreurs, les scientifiques des matériaux et les équipes de construction permettra de découvrir la valeur cachée du carbone incorporé.
Australia’s parliament has passed legislation and is now committed to cutting carbon emissions by 43% by 2030 and to meeting net zero emissions by 2050. As one of the world’s biggest emitters per capita, Australia must now roll up its collective sleeves and get to work.
The nation’s largest construction companies and asset owners have set strong climate commitments and are making adjustments to their operations to achieve net zero emissions. The biggest roadblock to achieving net zero emissions is embodied carbon – the emissions generated during a building’s entire lifecycle.
What does a whole-of-life carbon look like?
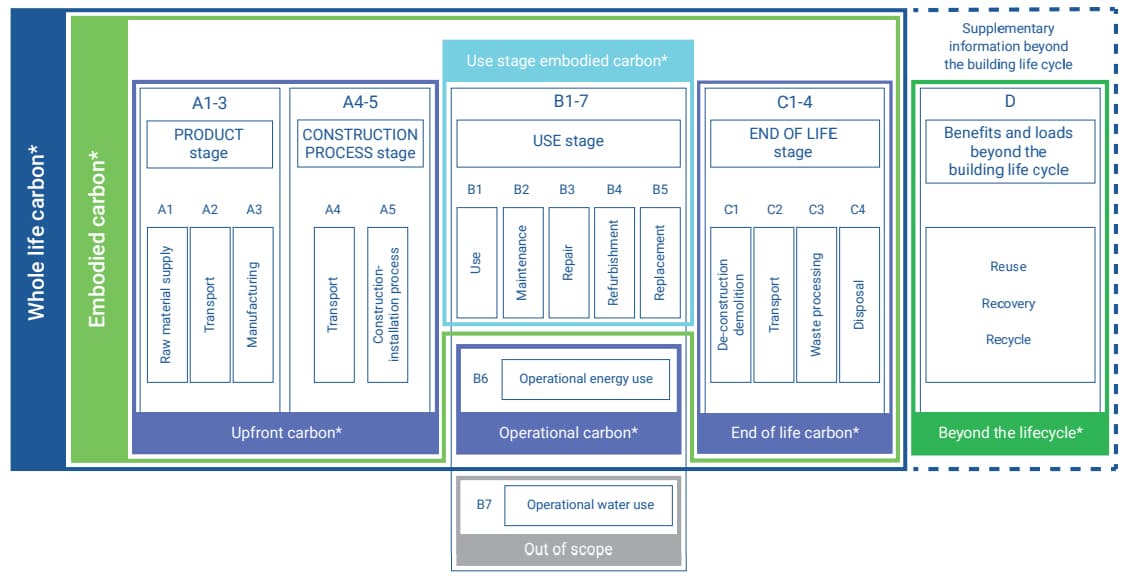
Source: World Green Building Council, Bringing Embodied Carbon Upfront
As Australia’s buildings become more efficient, the proportion of embodied carbon emissions will grow exponentially. In 2019, embodied carbon accounted for 16% of Australia’s built environment emissions. By 2050, the Green Building Council of Australia estimates this figure will rise to 85%.
In September the GPT Group pledged to measure and offset carbon emissions it generates on every new development – becoming the first Australian asset owner to do so. As Steve Ford, GPT’s Head of Sustainability and Energy notes, upfront carbon emissions “is within our control because we choose to undertake and pay for the developments”.
Measure, then manage
But how can Australia’s largest industry take systematic steps together to measure and manage the embodied carbon emissions on every development?
“We must start with a standard method of measurement for embodied carbon emissions,” says Niall McSweeney, Altus Group’s President of Cost & Project Management for Asia Pacific. Australia currently has no recognised framework to measure, benchmark or certify embodied carbon. A project is underway, led by the National Australian Built Environment Rating System, in collaboration with the Australian Institute of Quantity Surveyors and more than 100 other industry players, to develop new national standard for embodied carbon.
“But in the meantime, many companies are relying on benchmarking databases that are inconsistent and inaccurate,” Niall notes.
All new buildings seeking a Green Star rating must demonstrate a 10% reduction in embodied carbon against a benchmark building. By 2030, this will rise to a 40% reduction. “But to get a true and accurate calculation of a building’s embodied carbon, we must move beyond rating systems and benchmarking tools. We need very detailed measurement – and we need to agree what we are all measuring,” says Yang.
Testing builds trust
The Green Building Council of Australia is working with product manufacturers to build a materials database which will be freely available across the industry. A small number of product manufacturers have achieved Environmental Product Declarations which, like a label on the back of a cereal packet, disclose a range of metrics including carbon impact.
“But the only way we can be 100% sure of the carbon content of each material is to test it,” explains Altus Group’s Associate Director Zheng-Yang Ong. “We currently test for strength – sending away samples from every concrete pour to establish true strength – and we may begin to see random testing the carbon content of some products,” Niall adds. “I think we will eventually expect a clear identification of carbon as it relates to the quality of each product. The label will read: ‘This piece of steel is of x grade and its carbon content is y.'
Frameworks, product declarations and clear methods of measurement will build trust. But where is the trendline pointing? Yang suggests a new era of collaboration is ahead as “quantity surveyors, material scientists and construction teams work together to understand embodied carbon as a new measure of value”.
Auteurs
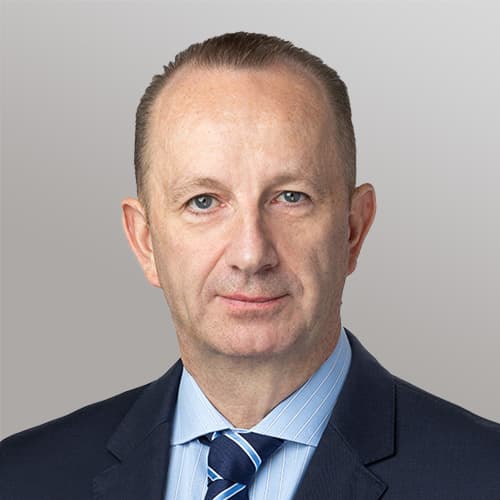
Niall McSweeney
Responsable du conseil en développement pour la région Asie-Pacifique
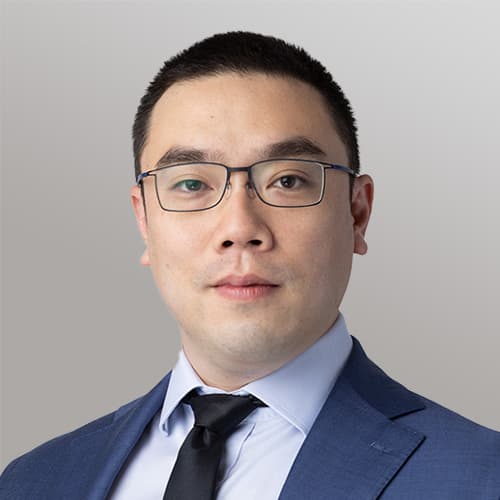
Yang Ong
Directeur associé
Auteurs
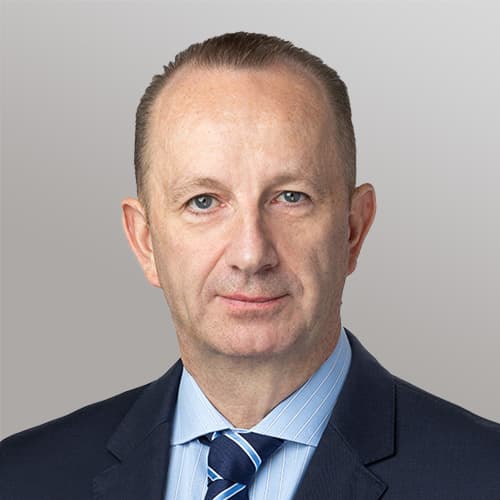
Niall McSweeney
Responsable du conseil en développement pour la région Asie-Pacifique
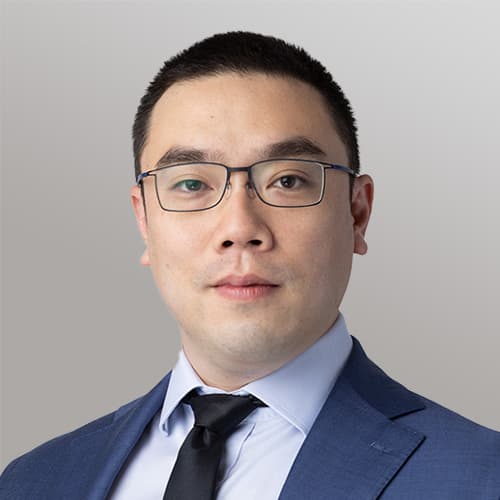
Yang Ong
Directeur associé
Ressources
Dernières informations
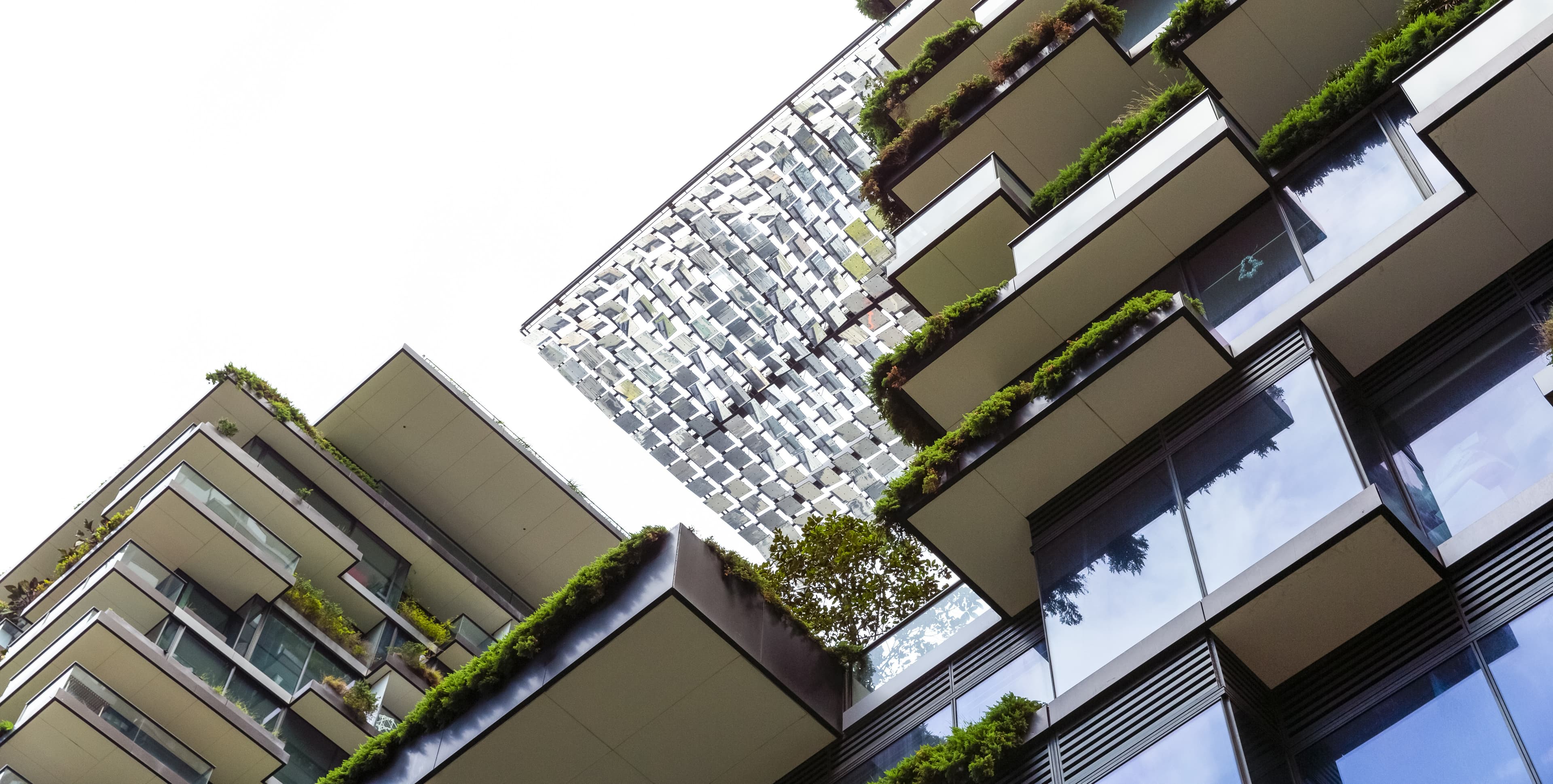
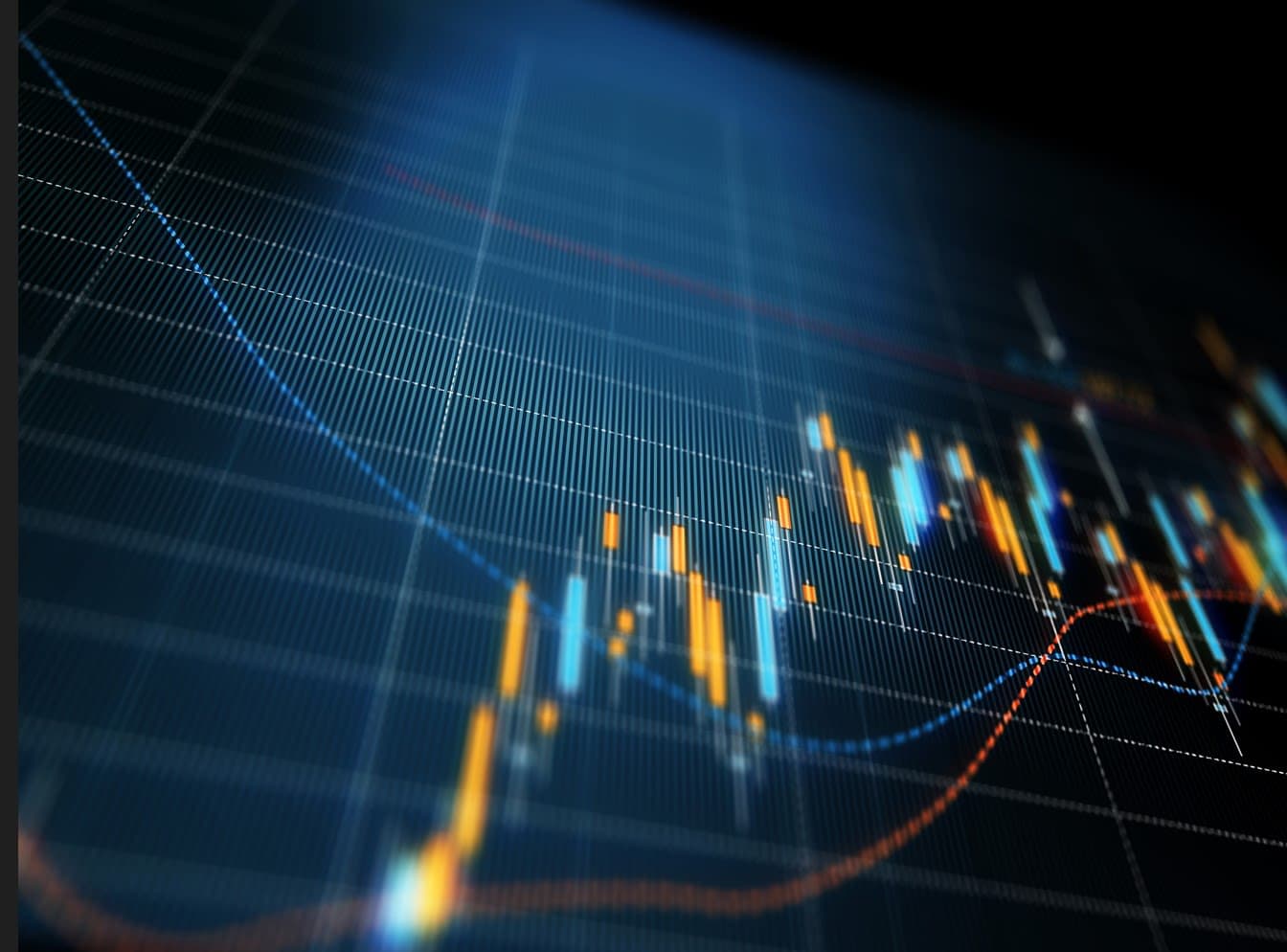
avr. 23, 2025
Réutilisation adaptative : un changement de mentalité, pas seulement de méthode
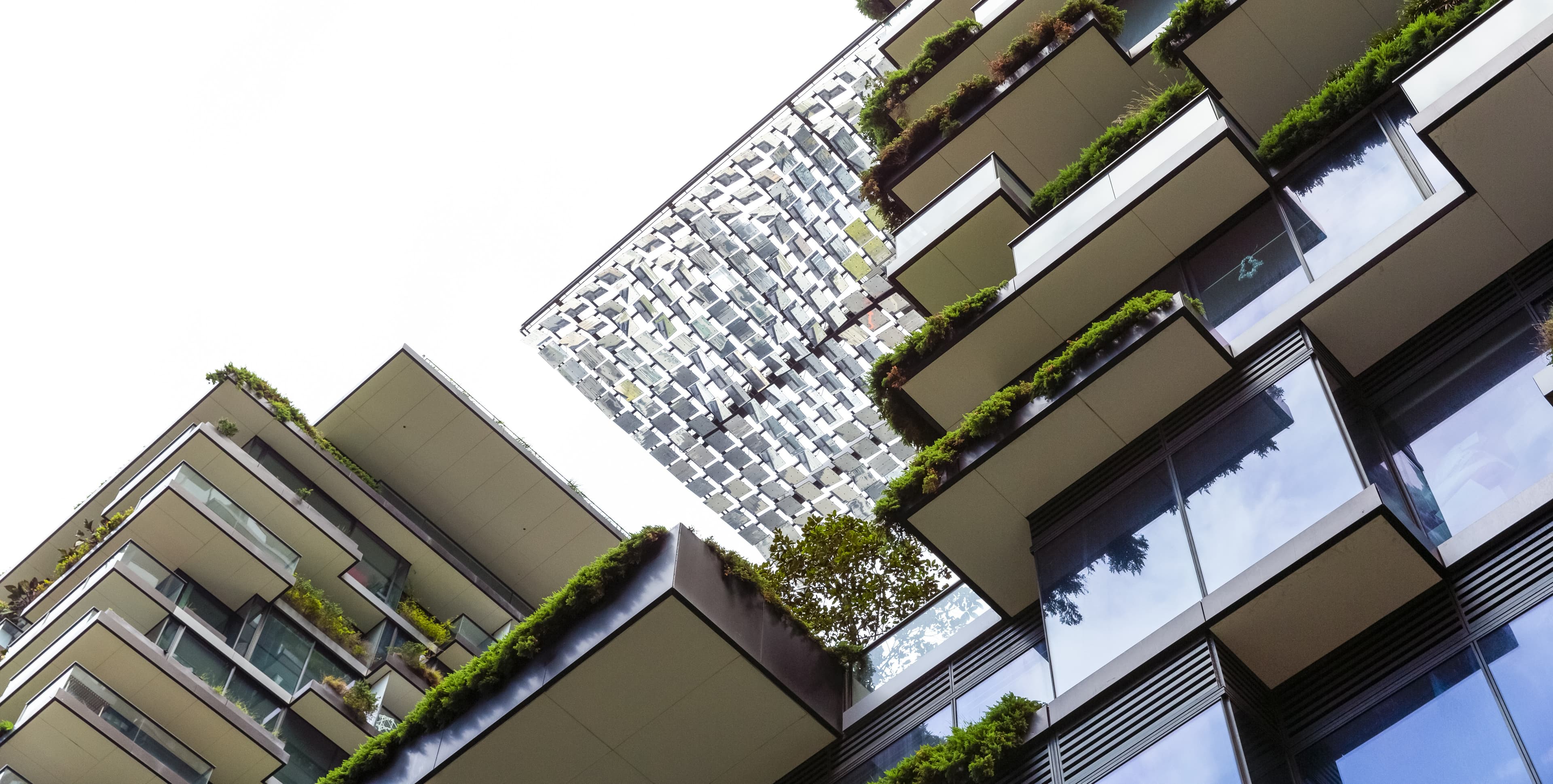
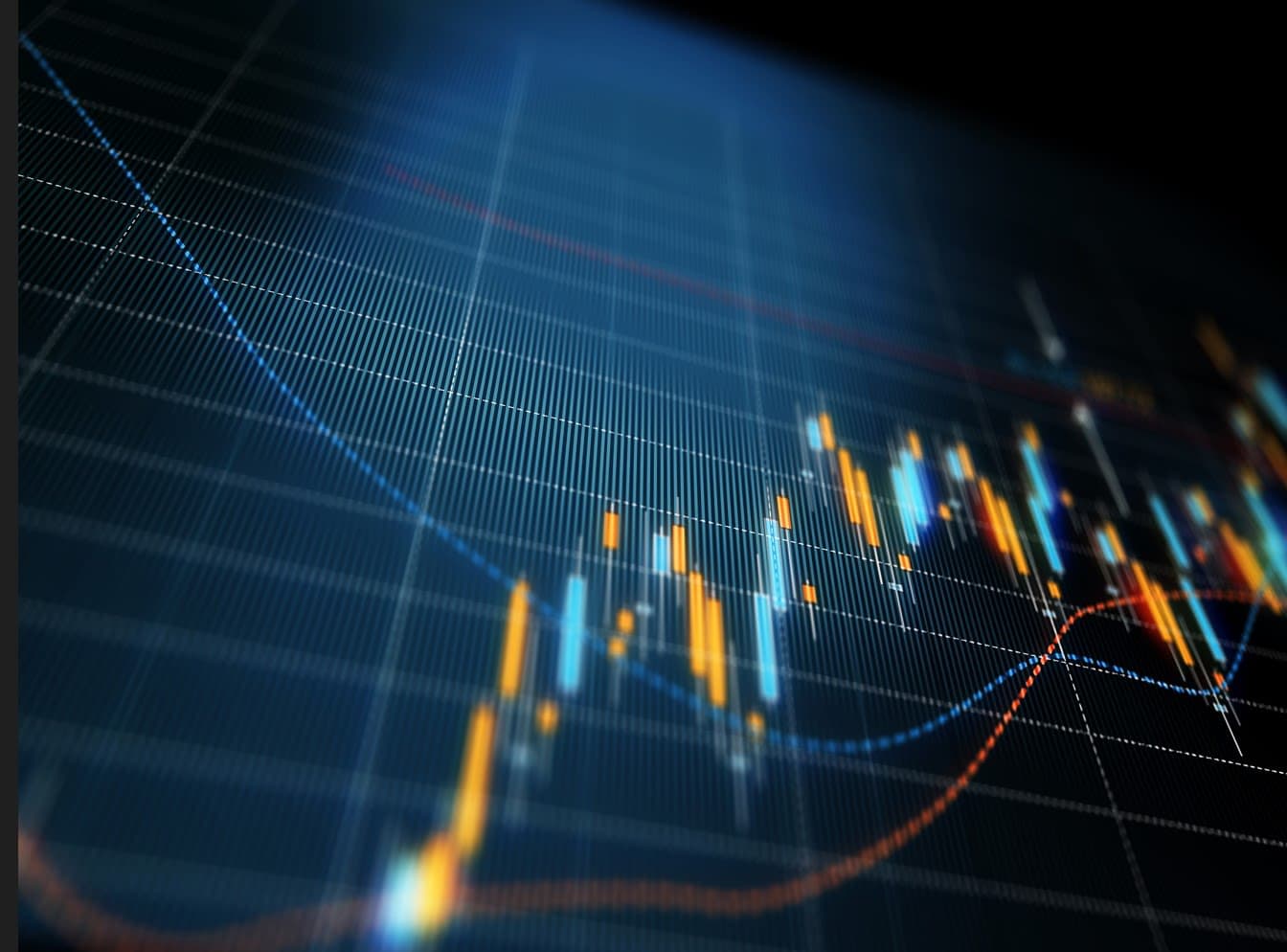
avr. 23, 2025
Réutilisation adaptative : un changement de mentalité, pas seulement de méthode
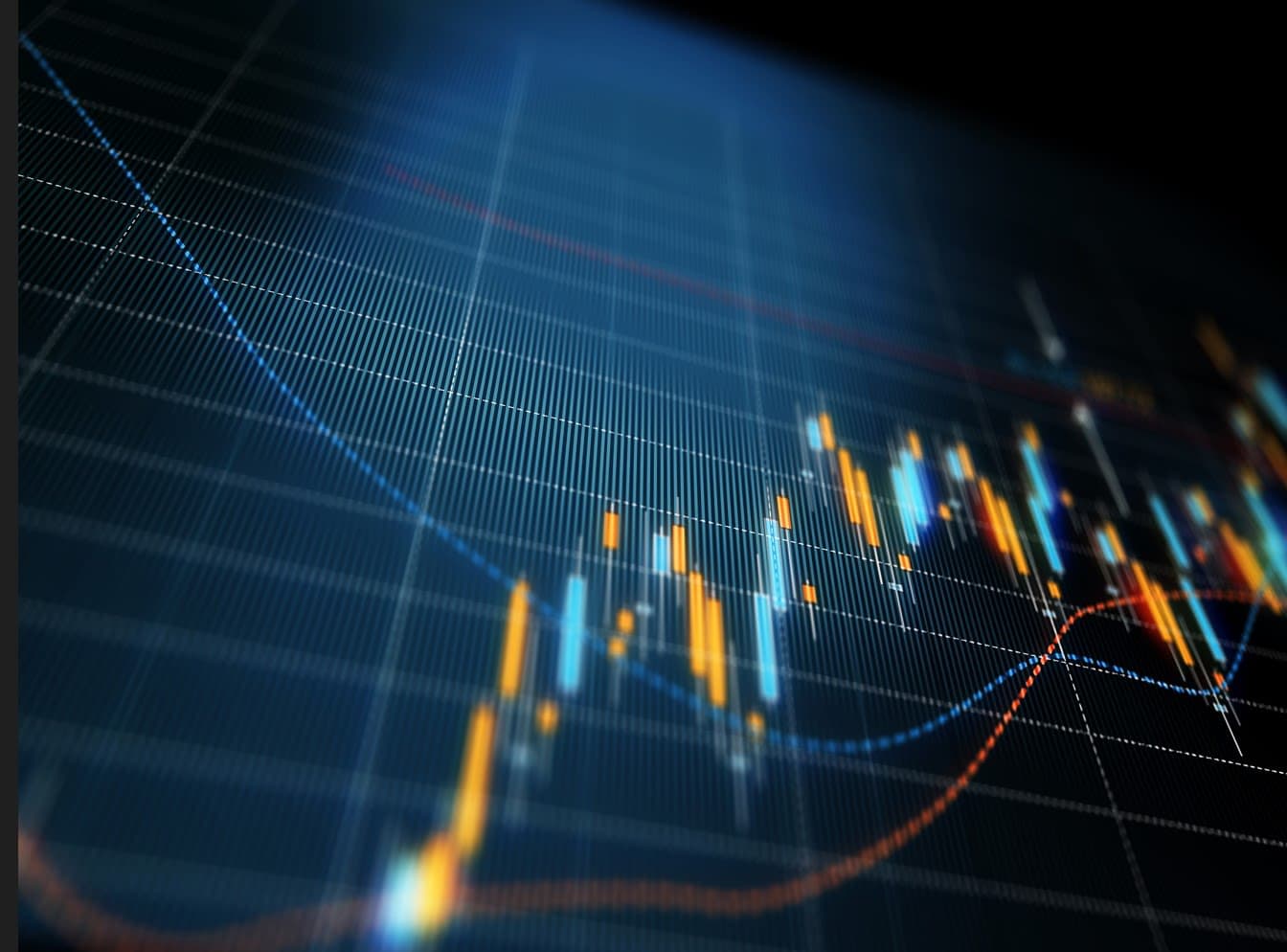
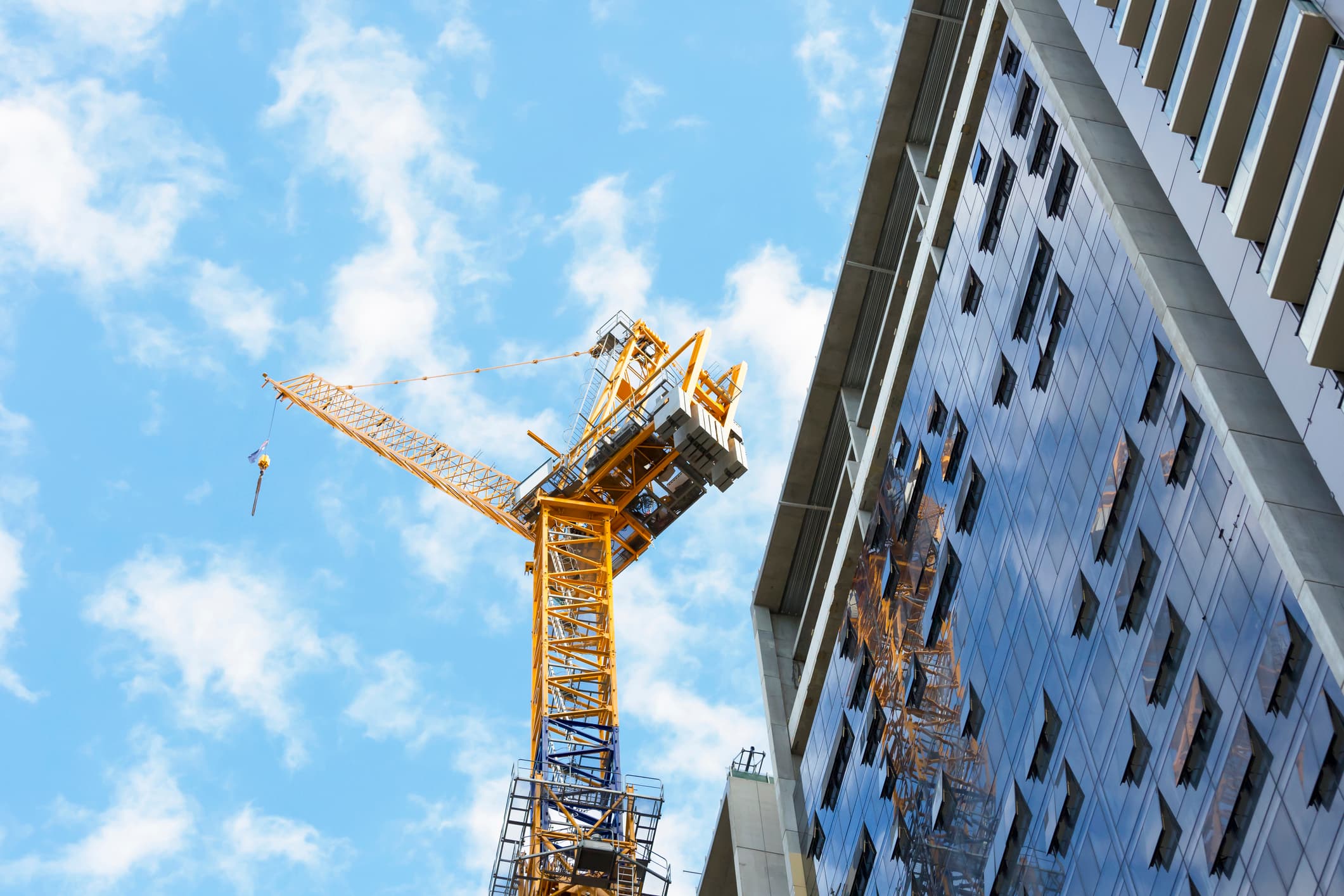
janv. 9, 2025
Construire l’avenir – Les principales tendances qui façonneront le secteur de la construction en Australie en 2025
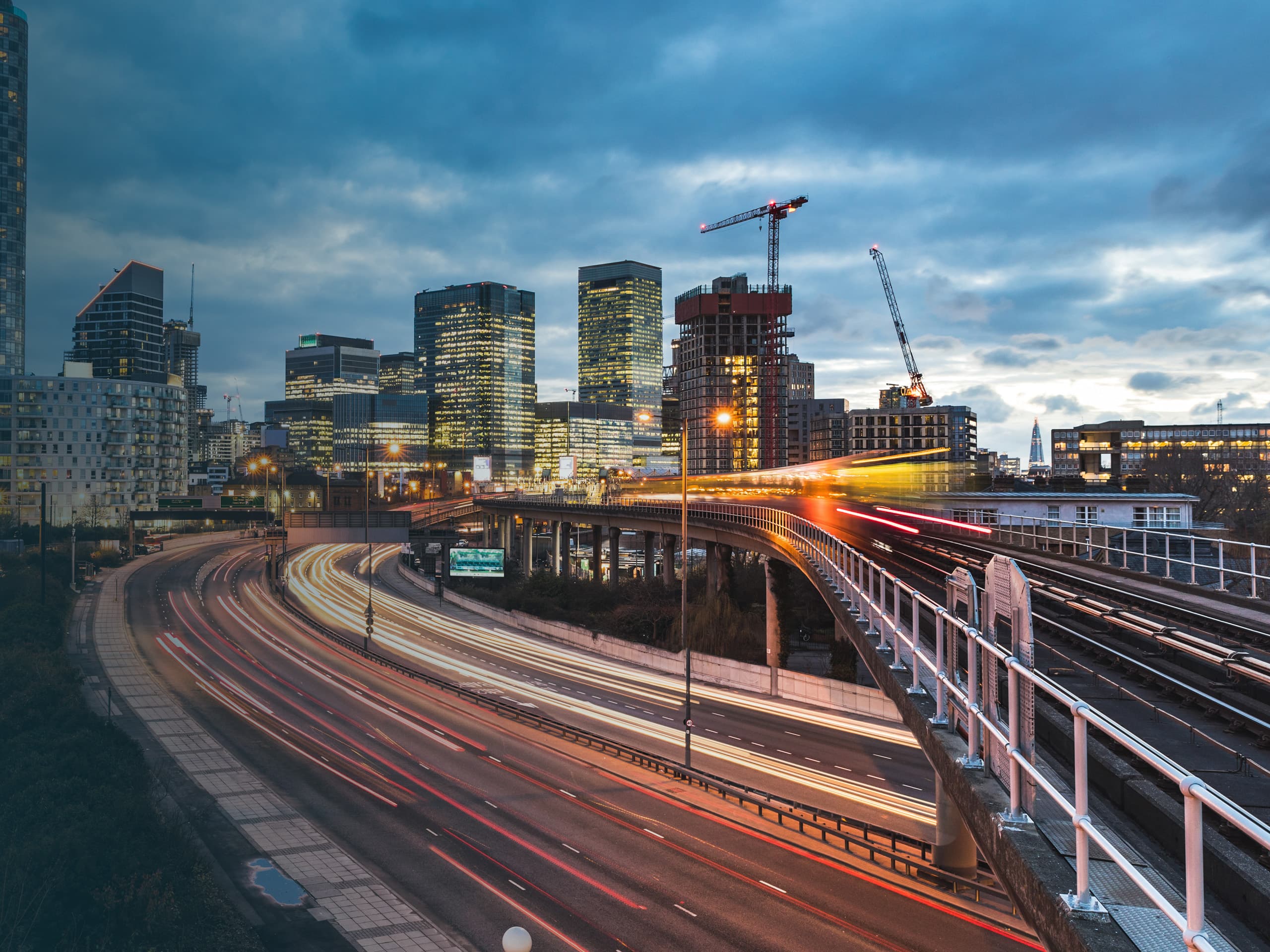
déc. 4, 2024